From Vision to Masterpiece: Inside Jaeger-LeCoultre’s Horological Haven
When you think of Switzerland, what comes to mind? Is it the snowy Swiss Alps, the beautiful green rolling hills, the fresh country air? You would certainly be right to think this, as this is precisely what we experienced on our latest trip to Switzerland. While the Watch Advice team was in Geneva to cover Geneva Watch Days, we also had the opportunity to head into the Swiss Jura and into the Vallèe de Joux.
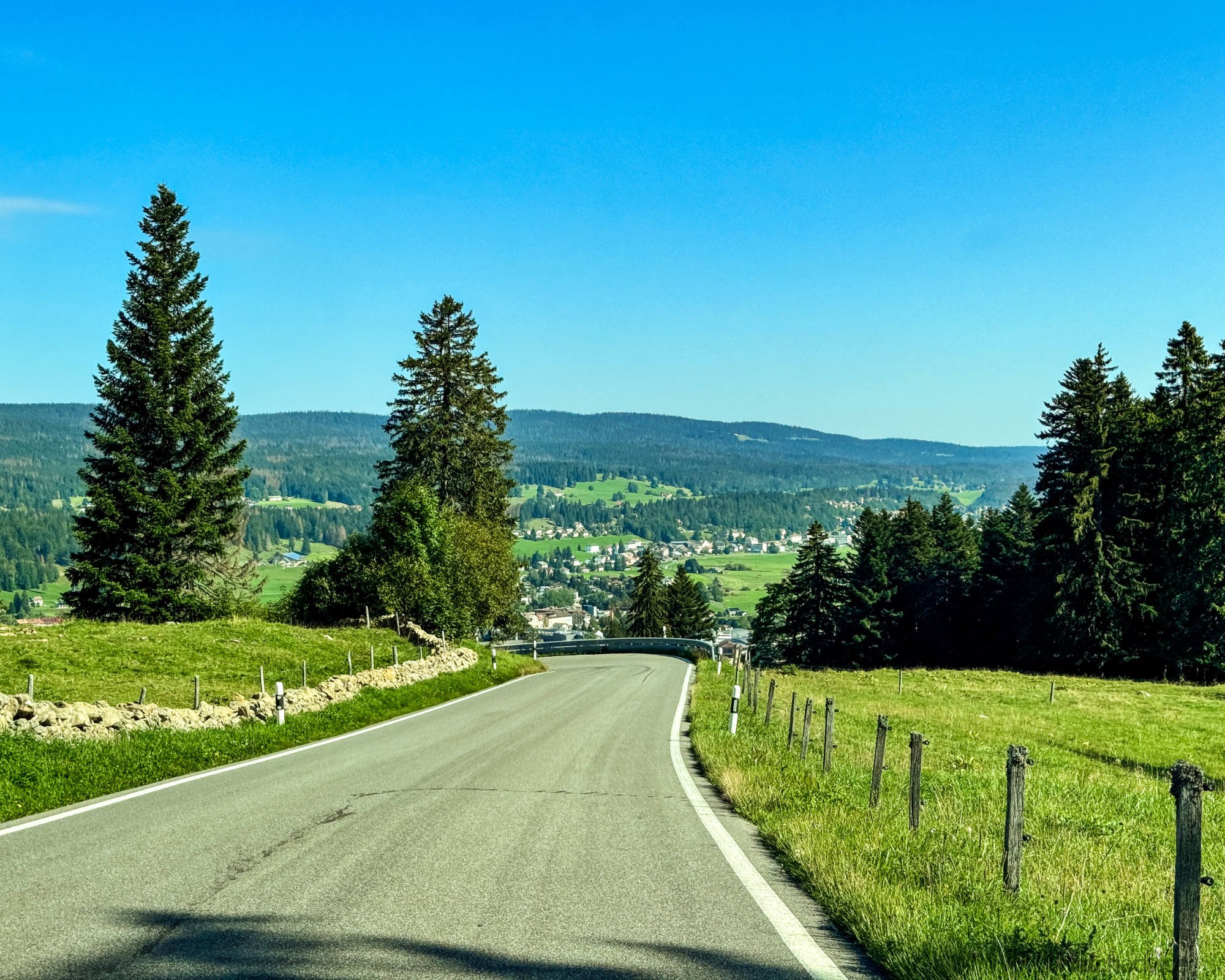
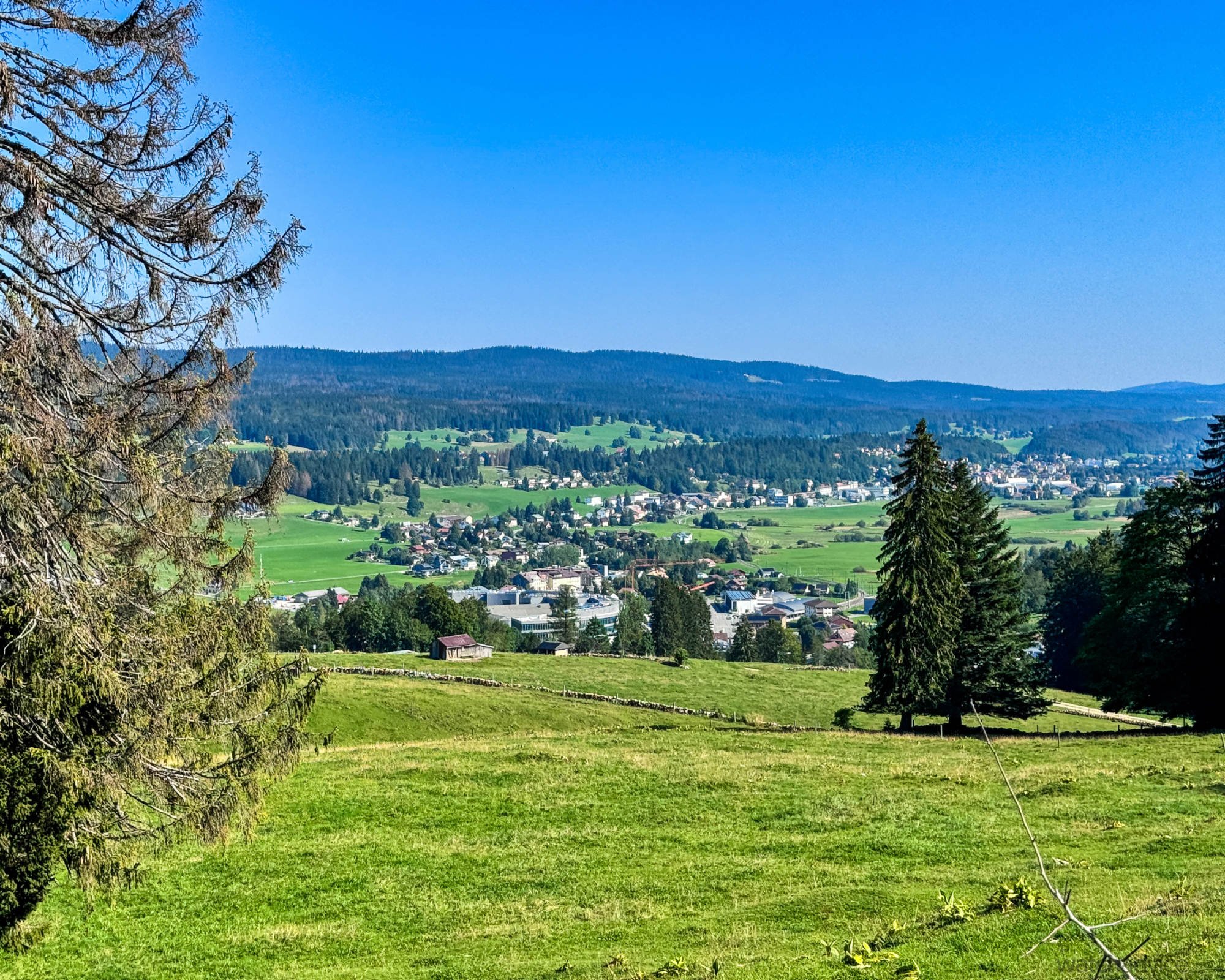
As we made our way out of the hustle and bustle of Geneva and drove about an hour into the Swiss countryside, our perspective on life did change. They say that humans tend to be happier when we are more exposed to nature, and I found this to be very much the case. I was instantly happy as we drove through the countryside and saw the scenic side of Switzerland. We were there during summer, which in Switzerland, you experience 30-degree warmth that probably only lasts a month. It also brings with it lush green grass and warm summer breezes, and you can even hear the sound of cowbells ringing!
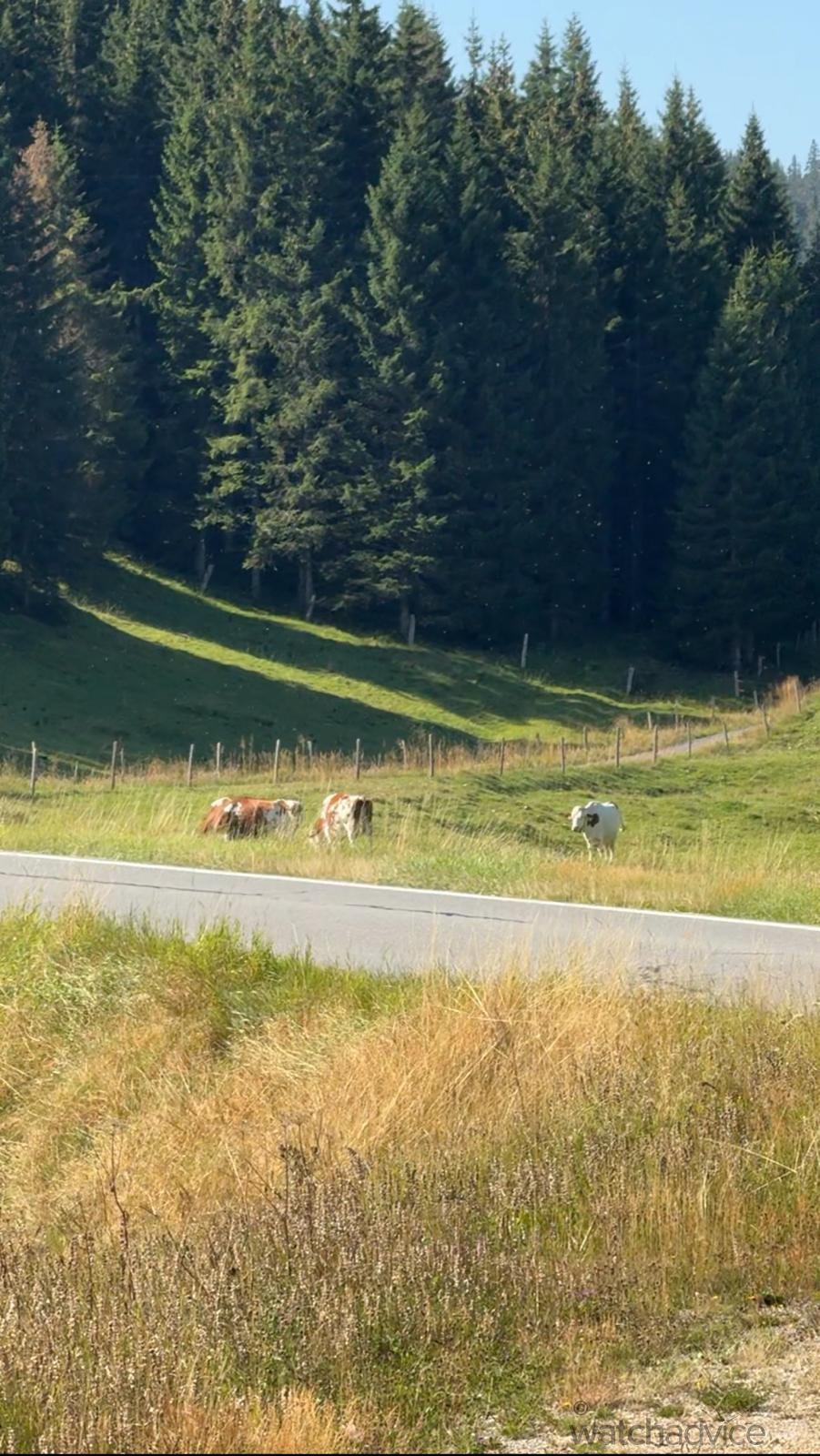
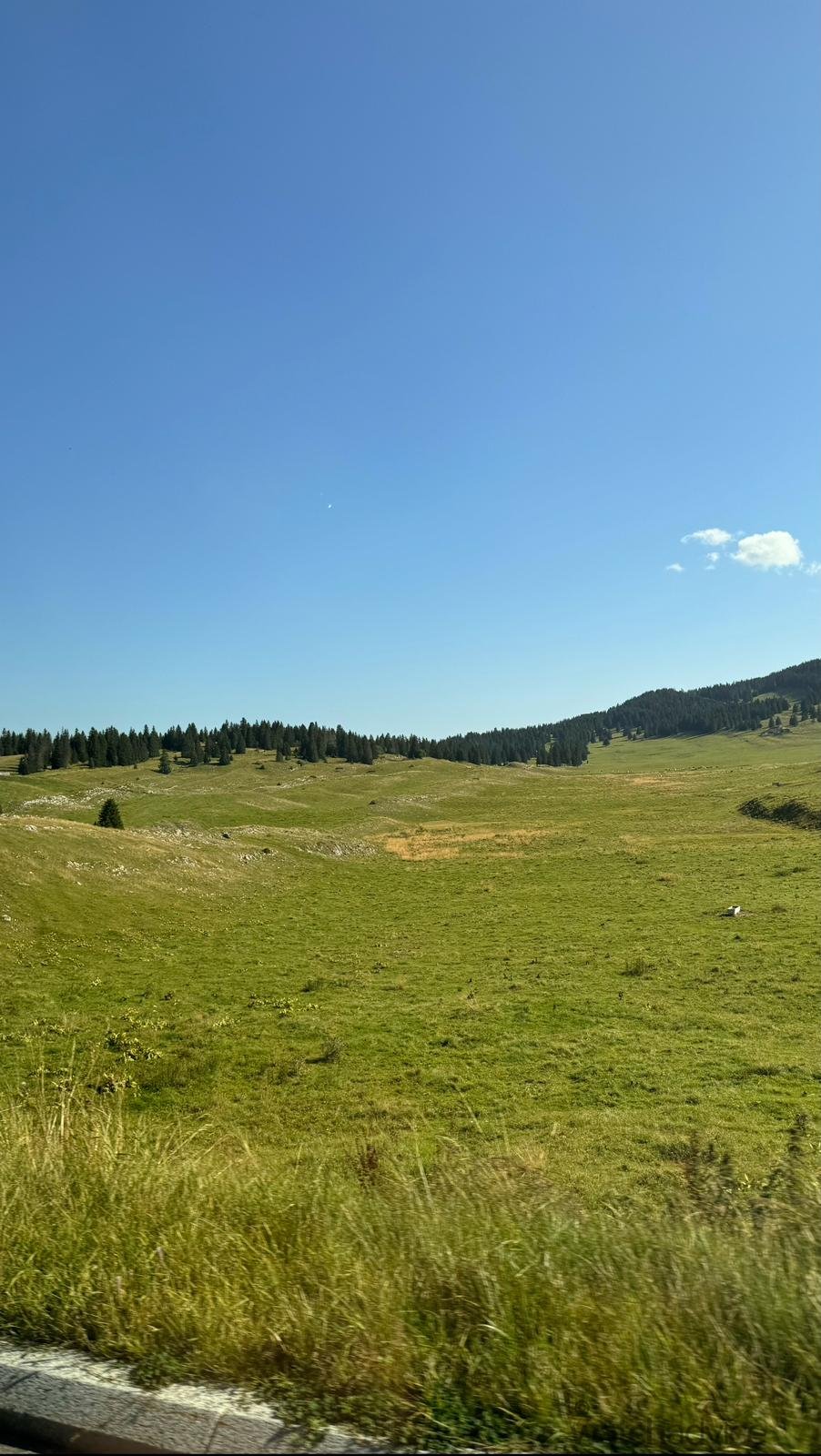
As we drove down the hills that are dotted with small towns, we arrived in the Vallèe de Joux and the small town of Le Chenit. It is said that, during the 17th century, watchmaking became widely spread throughout the Swiss Jura region – The Vallée de Joux in particular came to specialise in the field of Grande Complications, one of the noblest arts in watchmaking. For almost 100 years, almost all the ultra-complicated movements were completed in the Vallée de Joux. Add to this the fact the region is absolutely stunning in terms of natural beauty and scenic views; it would also serve as inspiration for the watchmakers to create beautiful mechanical art!
Located in the ever-so-beautiful Vallée de Joux, Jaeger-LeCoultre’s multi-storied manufacture stands proudly as a testament to the incredible watchmaking that goes on inside. Nestled in the Valley, the first thing you notice is the quiet. Other than the odd car that passes us on the road, the entry into Jaeger-LeCoultre epitomises the journey we took to get there. Known as the “Grande Maison”, the Jaeger-LeCoultre Manufacture is quite the establishment. It features different buildings dedicated to the different watchmaking areas of the brand, along with a museum showing us an extensive history of the Grande Maison. This is one Manufacture that, if you aren’t careful, you can certainly get lost in!
The Jaeger-LeCoultre Manufacture is the birthplace of countless innovations that have helped shape the world of horology as we know it today. From the brand’s iconic Reverso to the intricate Atmos Clocks, Jaeger-LeCoultre has continually pushed the boundaries of watchmaking. A visit to this horological heaven is simply more than just a tour. It represents the heart of Swiss watchmaking, where the past, present and future converge to the sound of ticking watches.
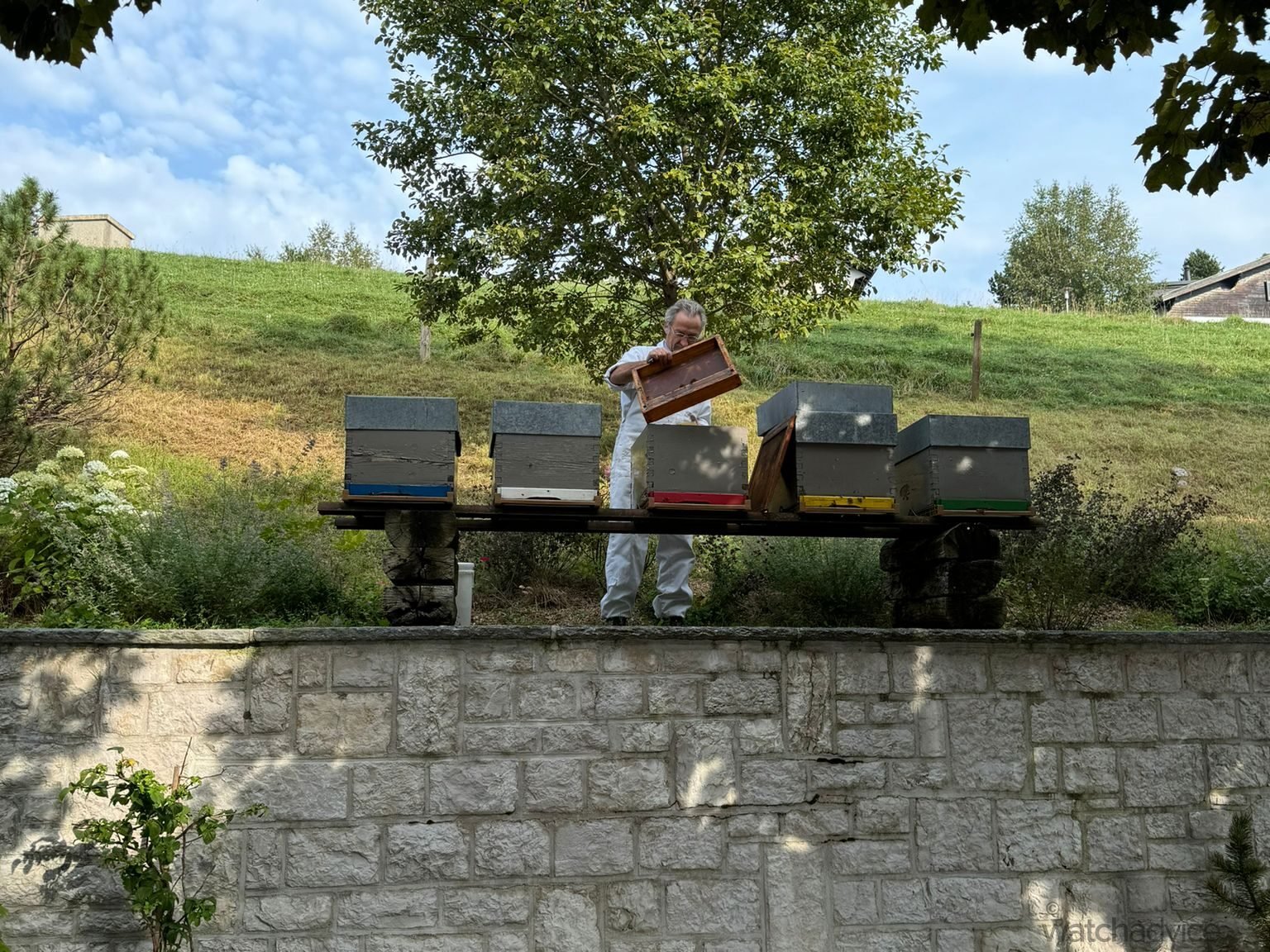
Before even entering the manufacture, I was quite impressed as I got to see a beekeeper busy extracting honey. This already shows Jaeger-LeCoultre’s commitment to local sustainability to use their own produce and products that is sourced from the local surrounding regions. Without even starting the Jaeger-LeCoultre Manufacture tour, I was already getting the sense of how the brand operates!
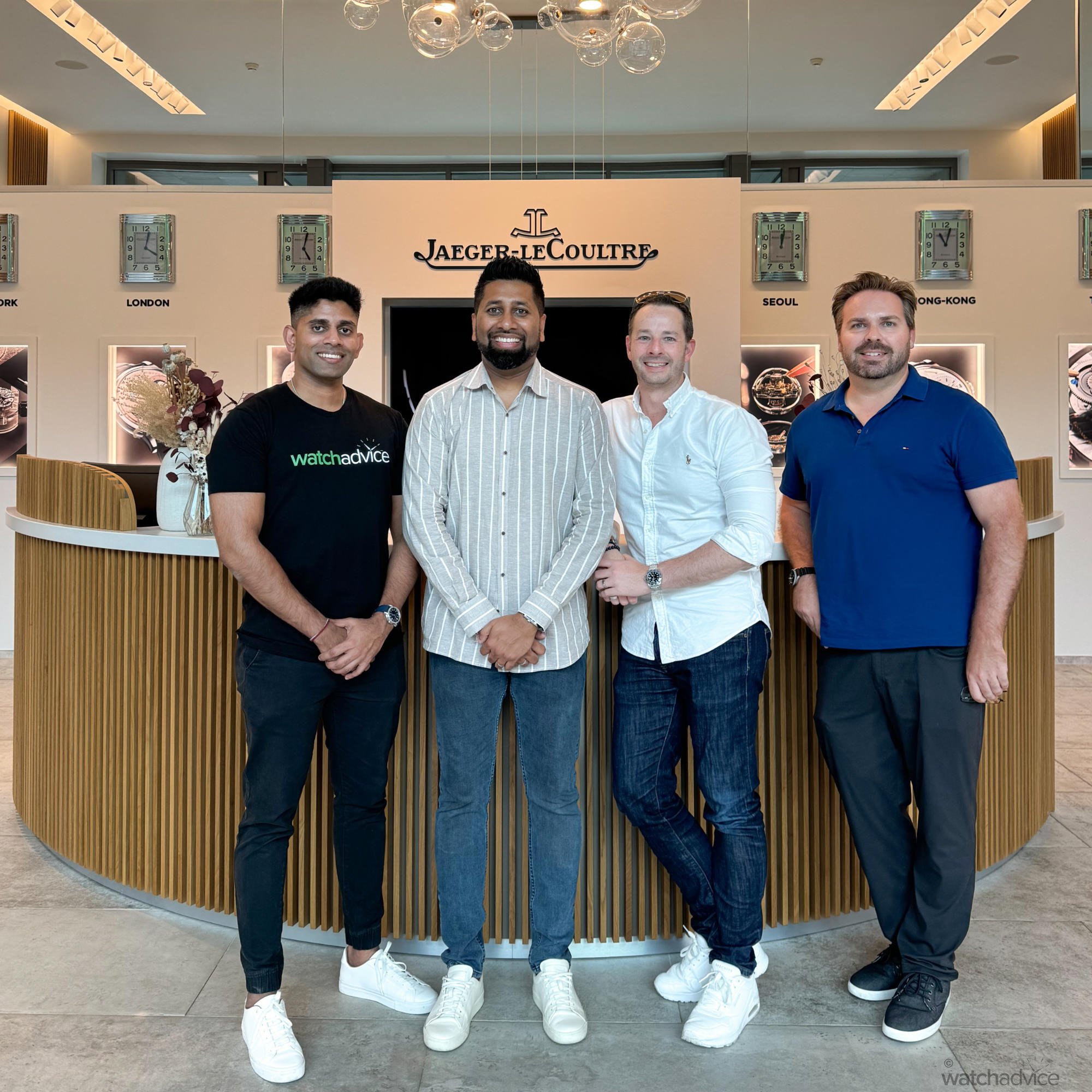
My journey into the Jaeger-LeCoultre Manufacture started with meeting the team who would take us on the guided tour. I was there alongside Chamath and Matt from Watchadvice, and we were certainly fortunate to be on the only ones on the tour, making it a more personal experience. We had the initial meet and greet with the Jaeger-LeCoultre team who would show us through the manufacture.
We were then guided to our first activity, which was an addition to the actual Jaeger-LeCoultre Manufacture visit. However, what I witnessed walking through the Jaeger-LeCoultre Manufacture were several photographs showing the past, present and future of Jaeger-LeCoutlre. A piece, or should I say a collection of photographs, that stood out for me was the wall that had several photos showing the Jaeger-LeCoultre Manufacture and its upgrades over the years. This was really interesting to see, as it showed the Jaeger-LeCoultre Manufacture from 1833 all the way to 2020, showing the progression of expansion through the decades!
We then arrived at the Atelier d’Antoine, a stunning room where precision watchmaking workshops occur. We, however, sat down to undertake the “Discovery Workshop – Stellar Odyssey”, which, in this case, is where we took a deep dive into the celestial side of watchmaking, understanding how moon phases, day and night indicators, annual calendars and perpetual calendars come about, along with the deep-rooted history behind each complication. There will be a separate article on this, where we will showcase Jaeger-LeCoultre’s celestial complications in detail, along with a deep dive into the workshop where we got to assemble our own perpetual calendar movement!
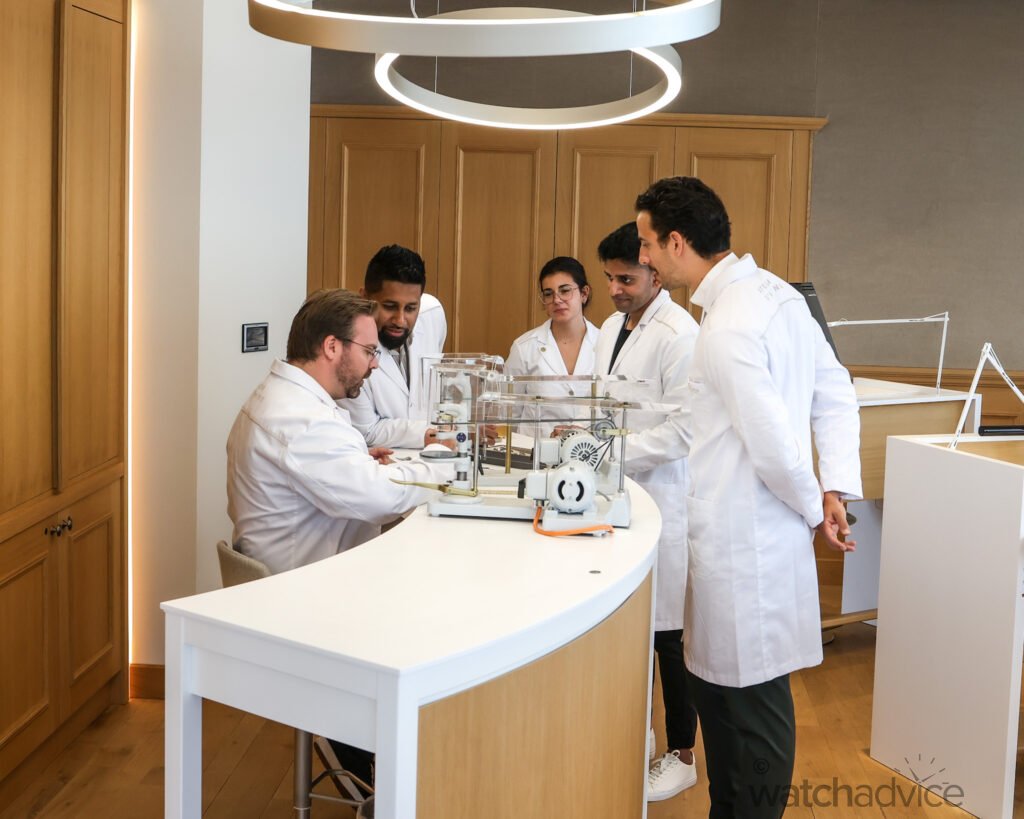
After the workshop, we were fitted into white cotton lab coats and headed to a workshop where movement finishing was completed. We were shown by a Jaeger-LeCoultre watchmaker the art of perlage finishing. Perlage finishing is a complicated finishing technique that is usually found on the baseplates or bridges of a movement and creates beautiful concentric circles. The simple explanation of the process of doing perlage finishing is when the machine “stamps” the plate and, when removed, leaves behind a circle. Watchmakers use a rotating abrasive rod, which is attached to a drill to “stamp” the plate.
While this is straightforward, it gets complicated from here on out. While it’s easy to do a single circle, it also comes down to how hard you press the drill onto the desired plate and how long you leave the drill pressed onto the plate. This is what I certainly noticed when I tried my hand at the perlage finishing technique. After you get the weight and length of pressing the drill right, then you have to complete the “pattern”, which for a watchmaker is putting one circle next to another with them slightly overlapping, and then doing this in large circular patterns to cover the plate as required.
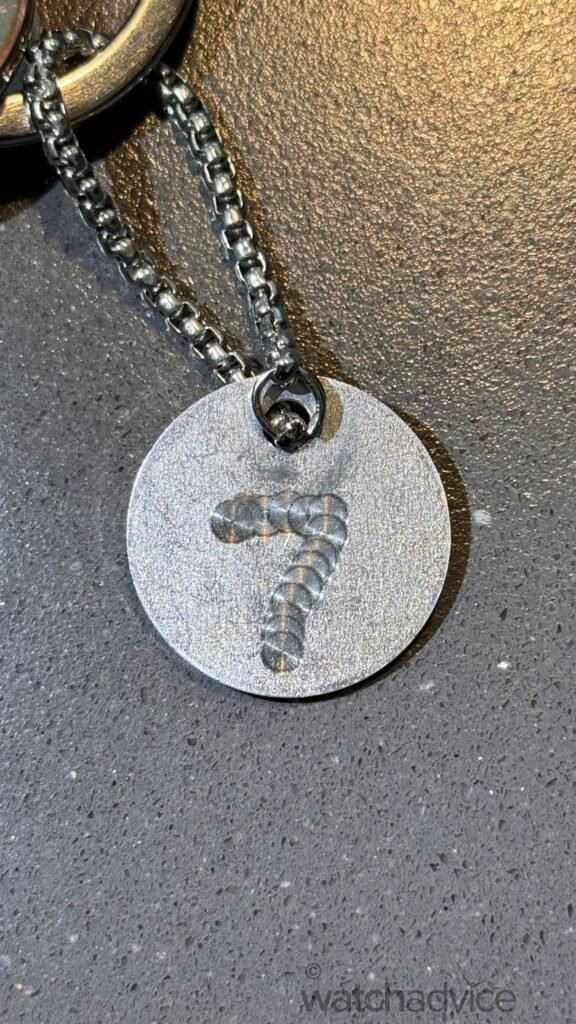
This is by no means an easy task, as when we each had our own turn at it, we quickly found out how hard it is to have the stamped circles overlaying on each other even in a straight line, let alone creating a full pattern! I opted to create my favourite number seven, and as you can see the weight was off initially due to the darker circles, and keeping it in a straight line was no easy task, even though it looks simple!
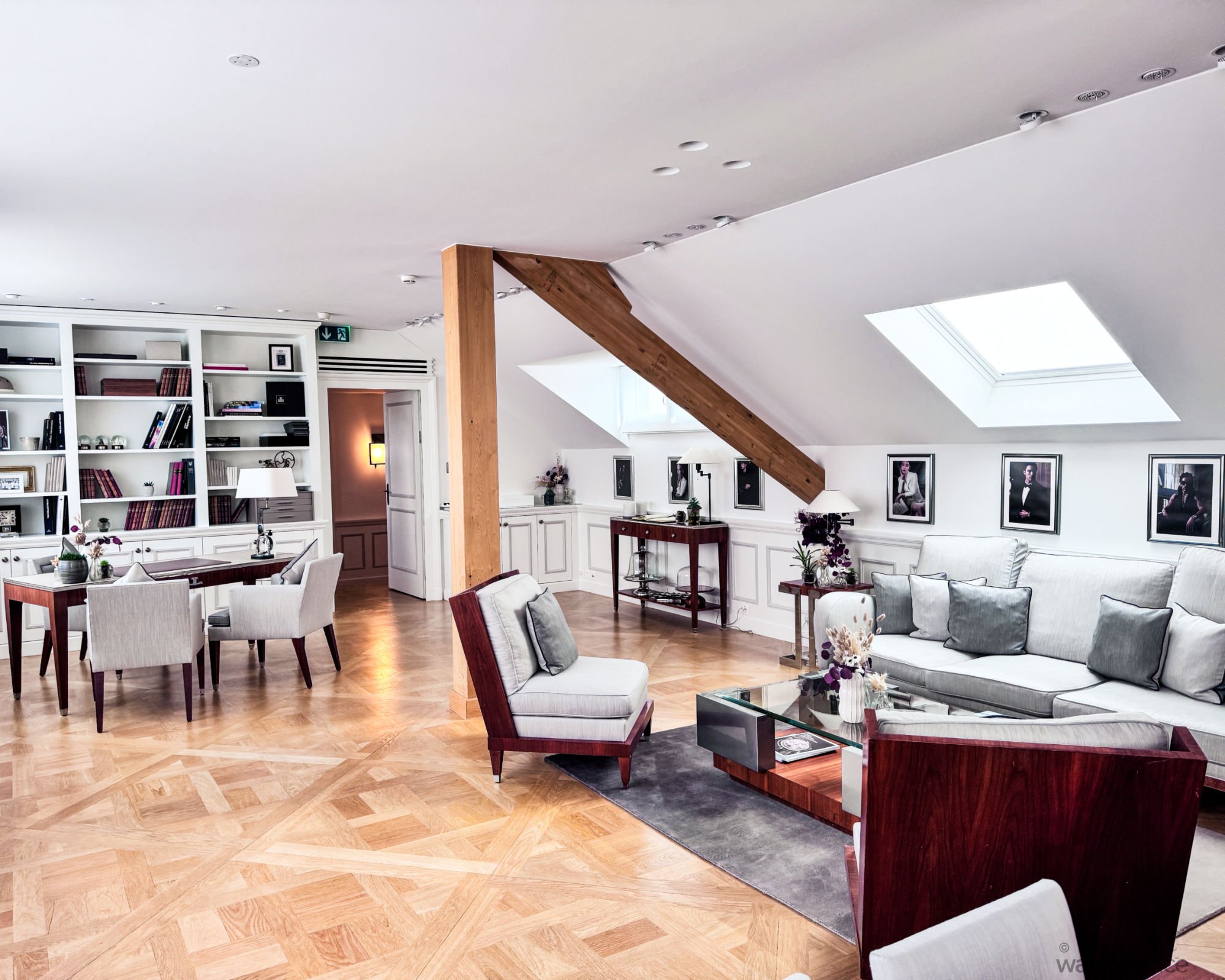
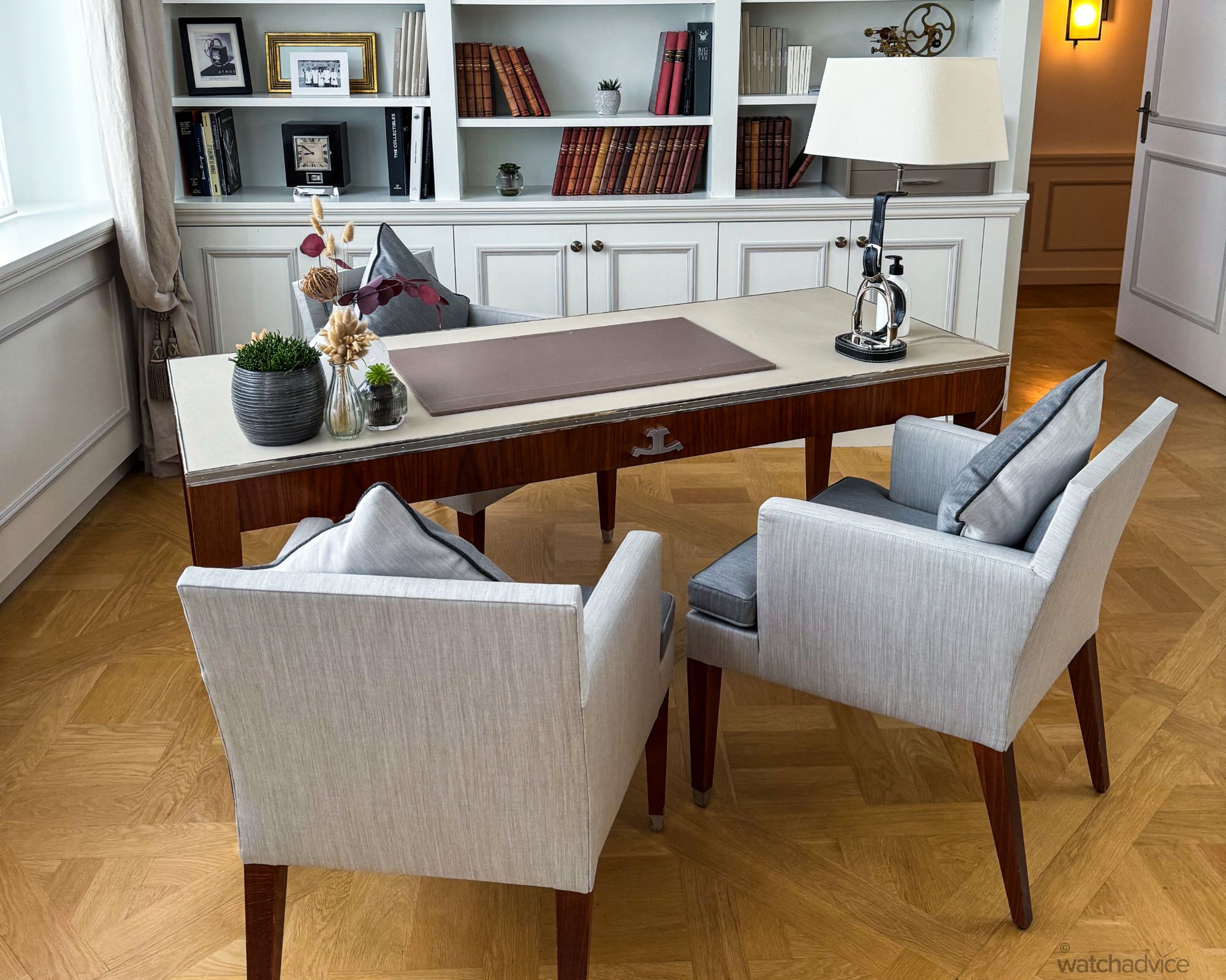
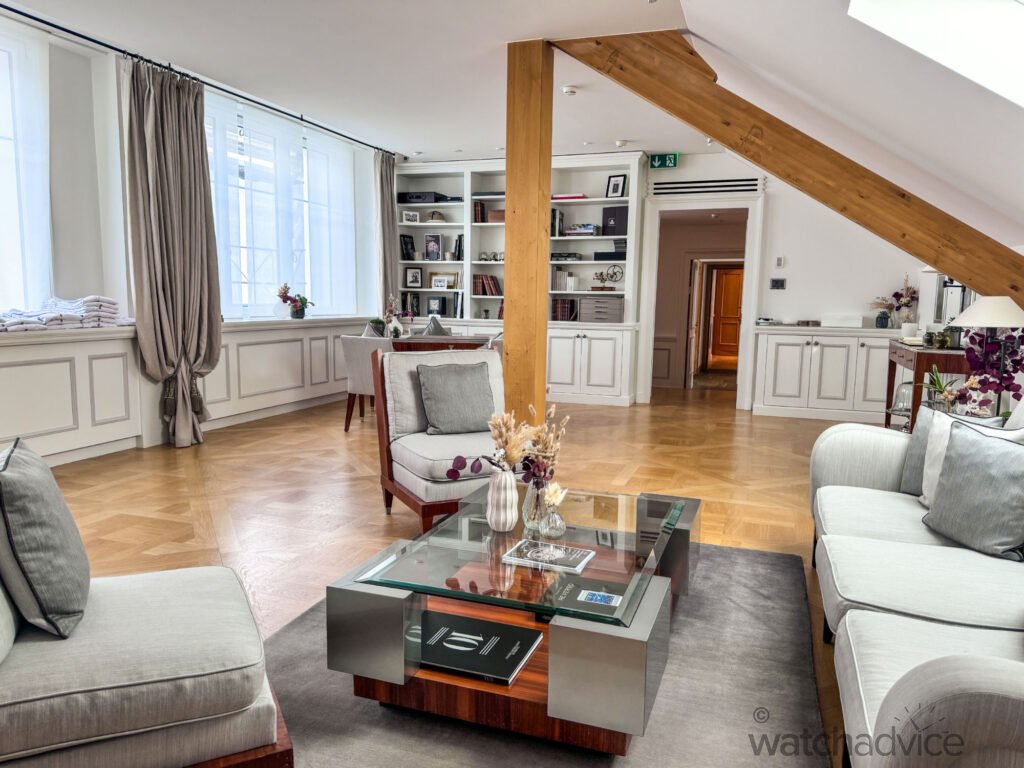
After the Perlage demonstration and workshop, we took a break, and that’s when we had time to explore the Jaeger-LeCoultre Manufacture at our own pleasure, restricted to the floor we were on; however, as the rest of the Manufacture we required the Jaeger-LeCoultre team. As we made our way through, we came across the Maison d’Antoine, where we would have lunch later (again, this was an extra part that was added for the Watch Advice team). This was when we came across the VIP Lounge, which, when opened…was jaw-dropping.
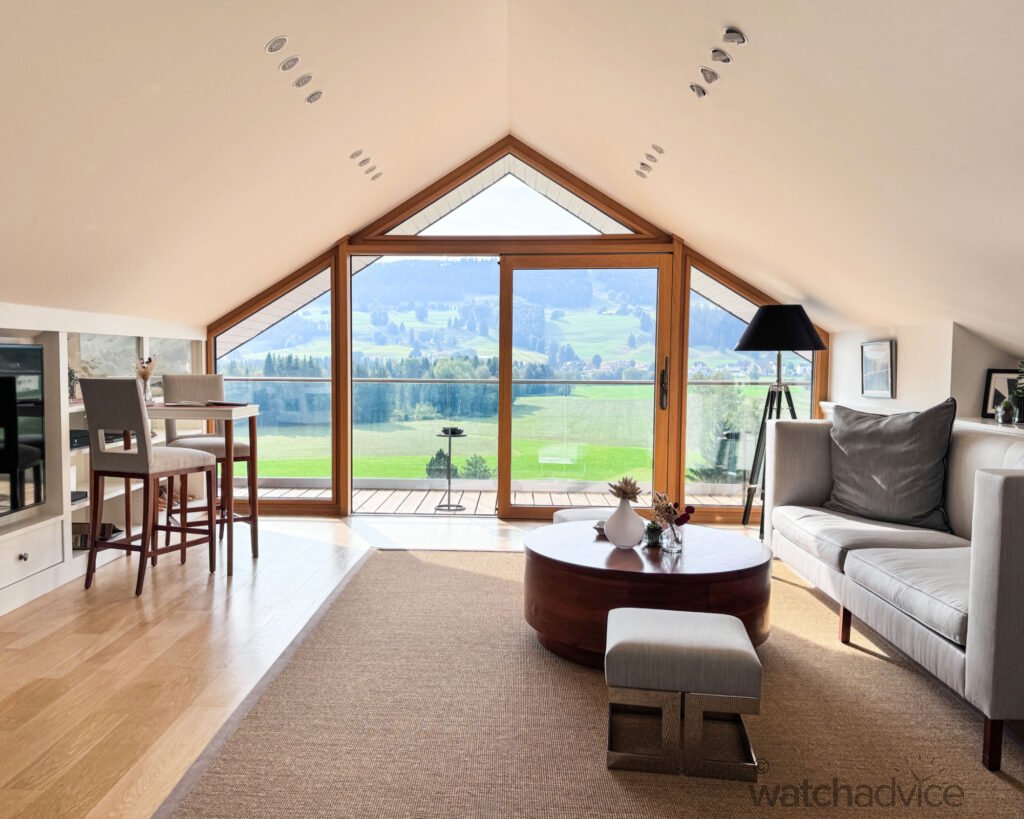
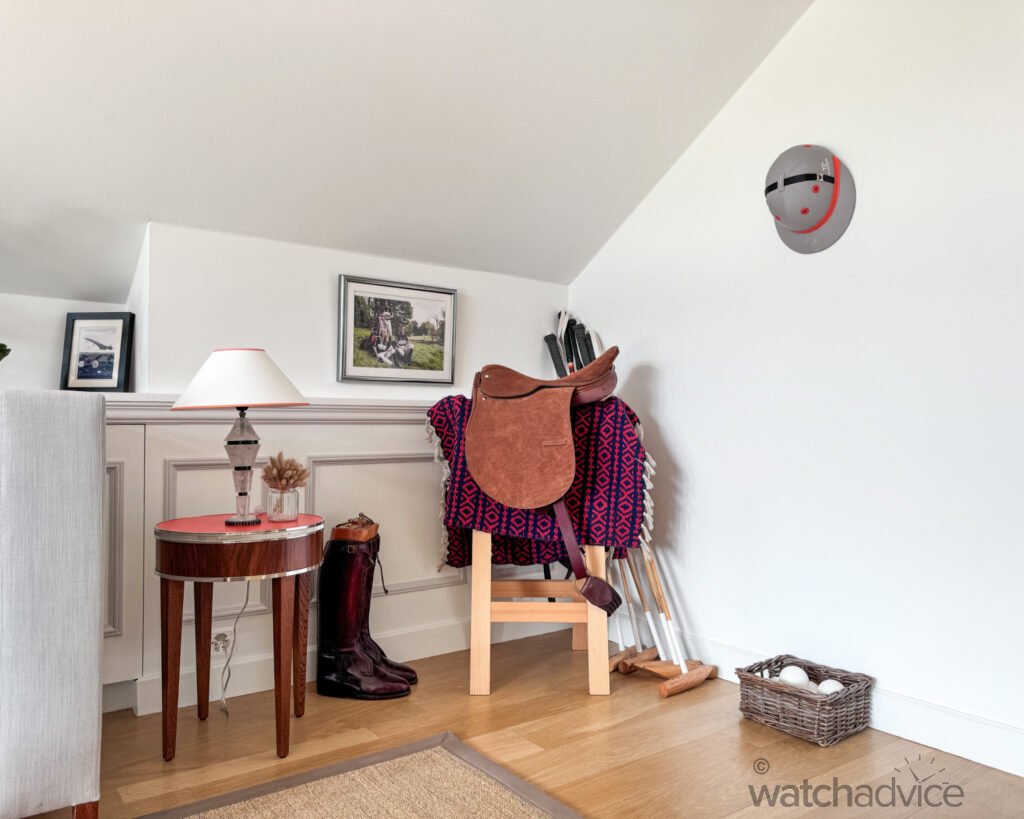
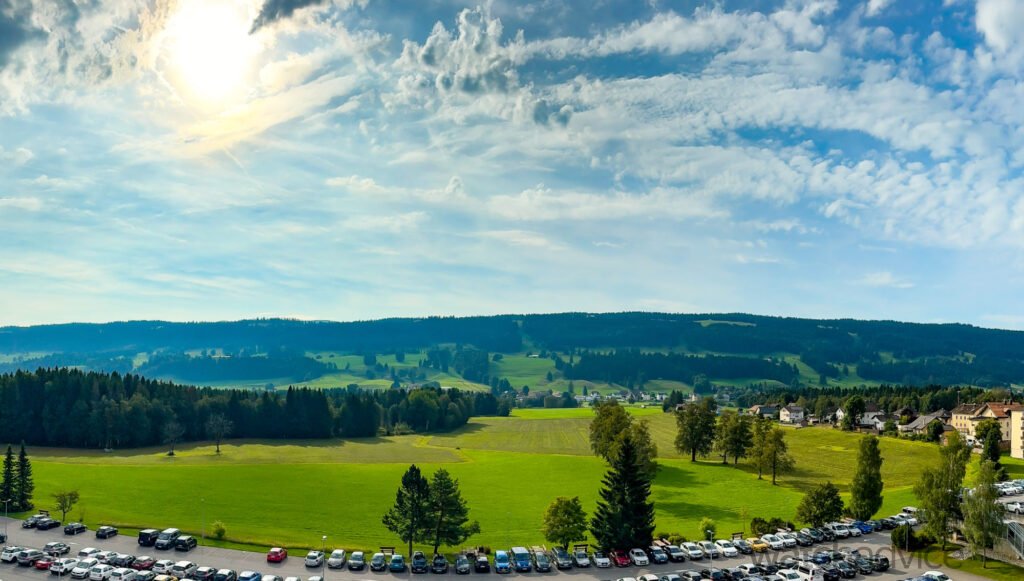
As soon as you open the door, you are greeted with large windows that go from one end of the room to the other and extend all the way to the top of the roof. The view through this room was just purely stunning. It’s hard to put into words what we felt the first time we opened the door, entered this room, and saw the view. It overlooks the stunning farmlands adjacent to the Tete Du Lac nature reserve, and the Jura mountains in the background. Imagine working alongside this view every day! Can certainly imagine being inspired to create some magic with Jaeger-LeCoultre timepieces!
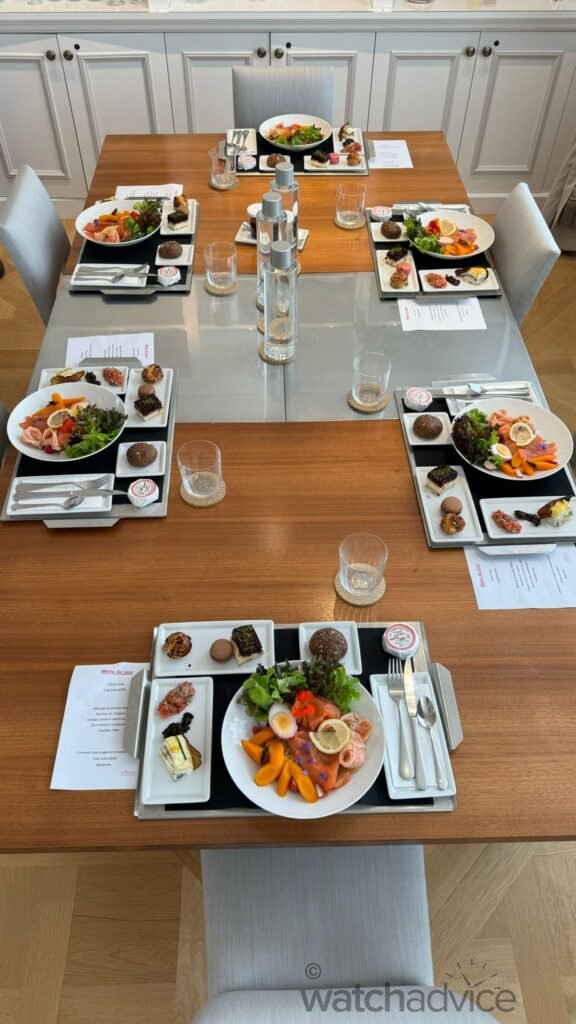
After we had some time to look around, we were then treated to lunch with Mathieu, the heritage director of Jaeger-LeCoultre. We were presented with a beautiful lunch that was all sourced locally from the surrounding farms, as well as the fish that was sourced from the nearby lakes. It was a great experience being able to eat alongside him and talk all things watches and Jaeger-LeCoultre. Certainly grateful for this experience!
After lunch, we started our second phase of the Jaeger-LeCoultre Manufacture! We were taken to the Heritage Gallery, where Jaeger-LeCoultre’s archives show us the brand’s rich history! The Heritage Gallery was created only a few years ago in 2017. If you want to know about the history of the Grande Maison, look no further than the Heritage Gallery, as the organised shelves of documents and records are presented in an eye-catching modern display. We had a separate dedicated guide for this section, which explained this history in quite detail.
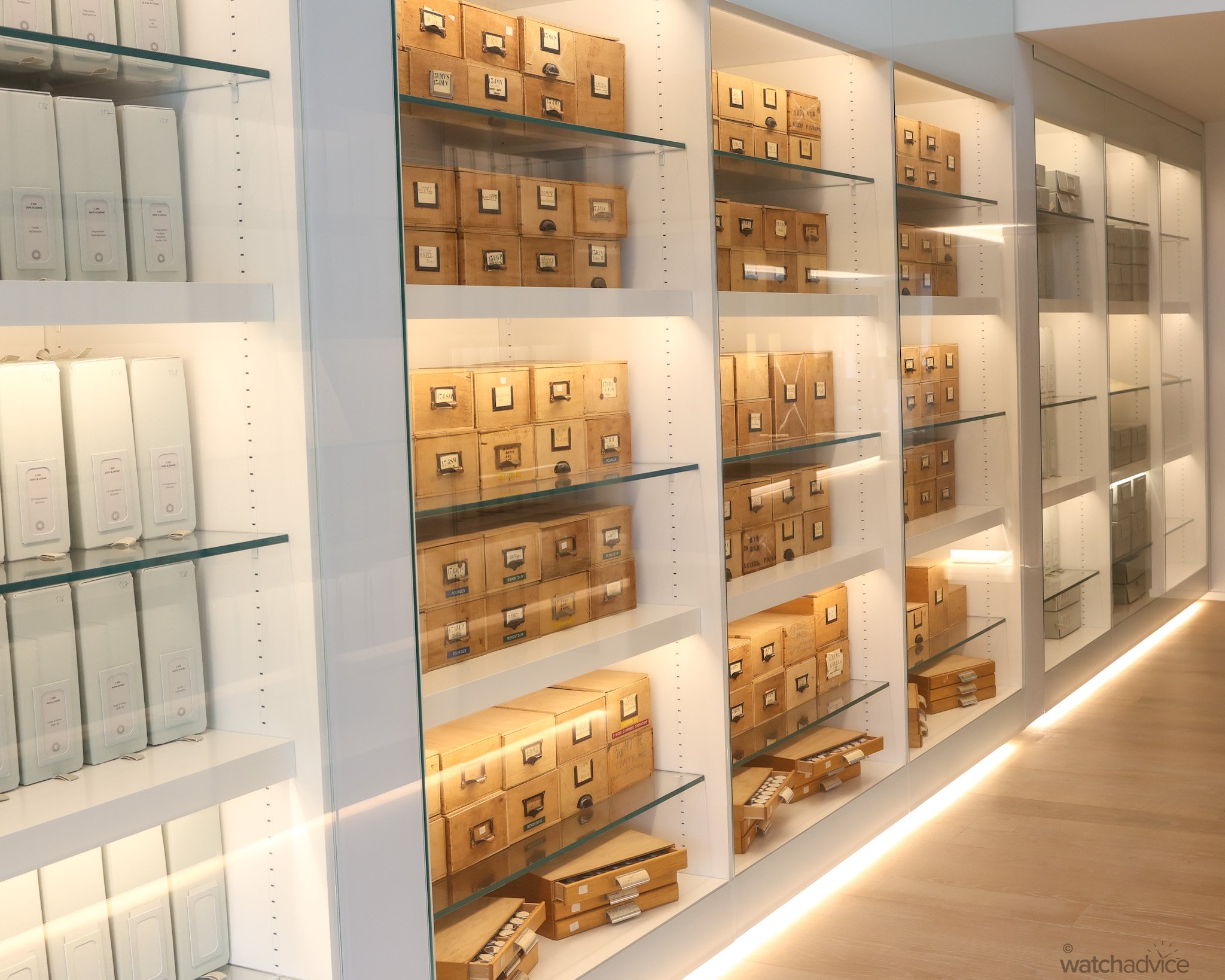
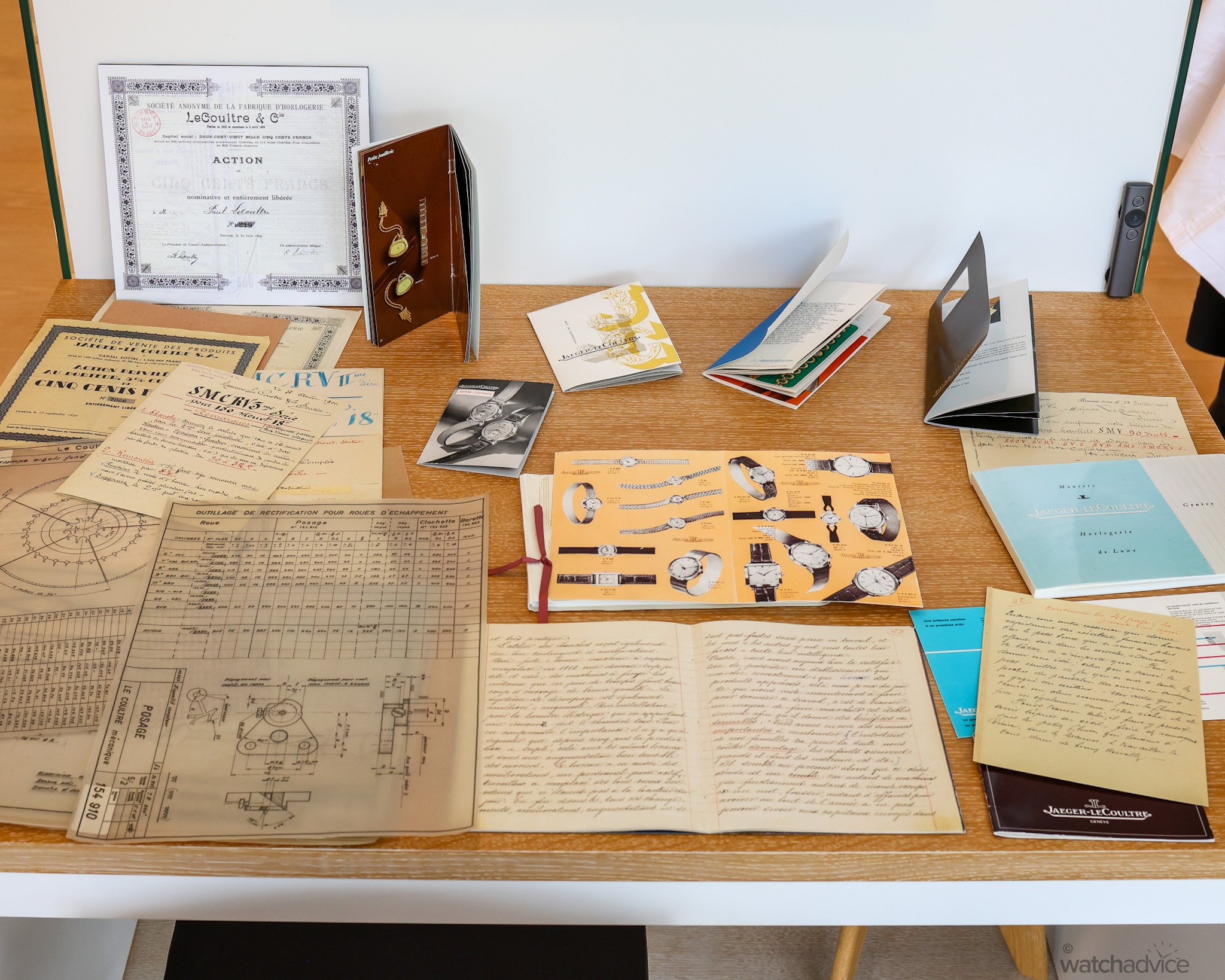
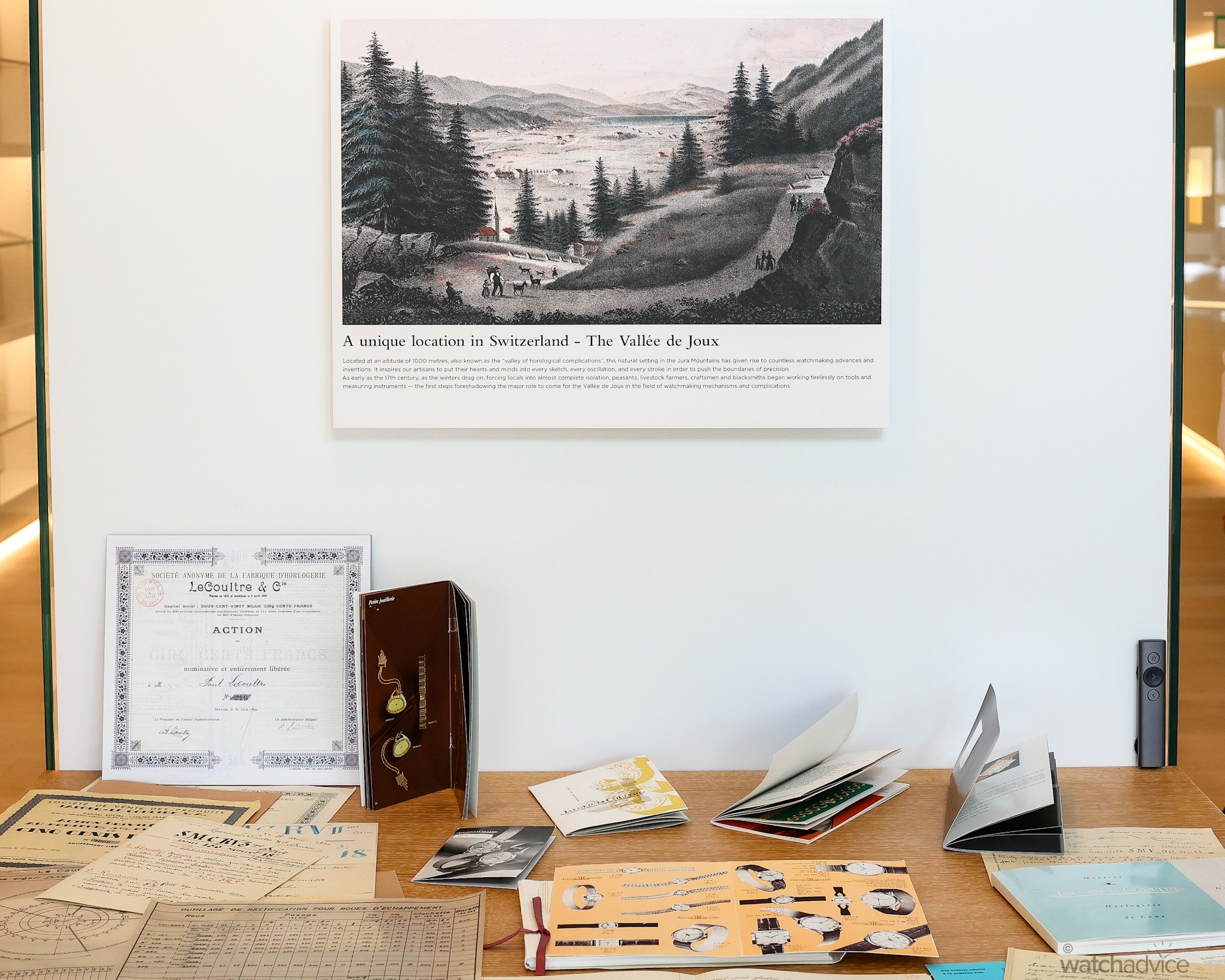
What we saw in this section of the manufacture was everything you can think off related to the brand’s history. The first pocket watch designs, the manufacture sheets, the purchase order books, how the location for the manufacture was initially chosen and even the family tree of LeCoultre! There was too much information and too little time to go through it all!
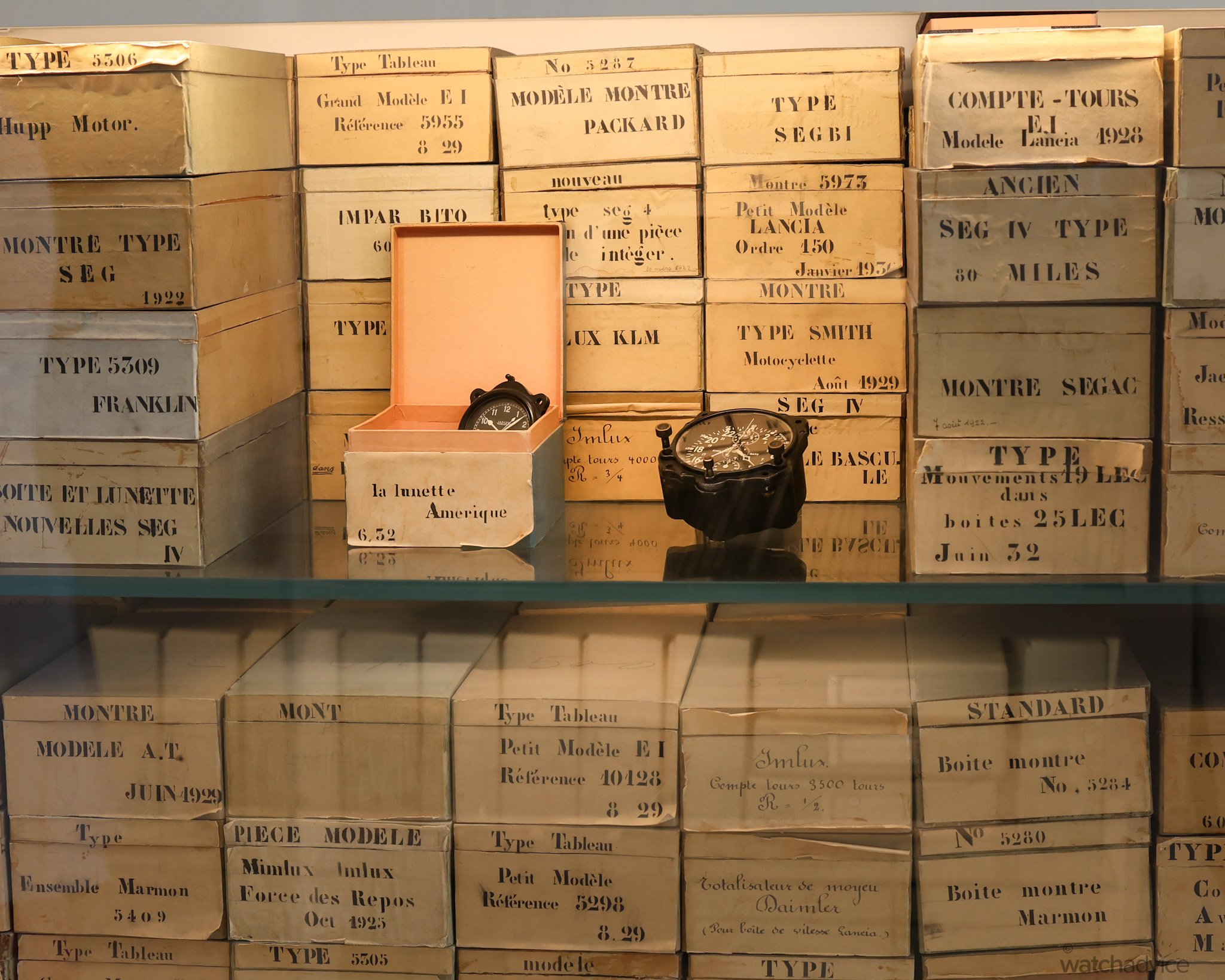
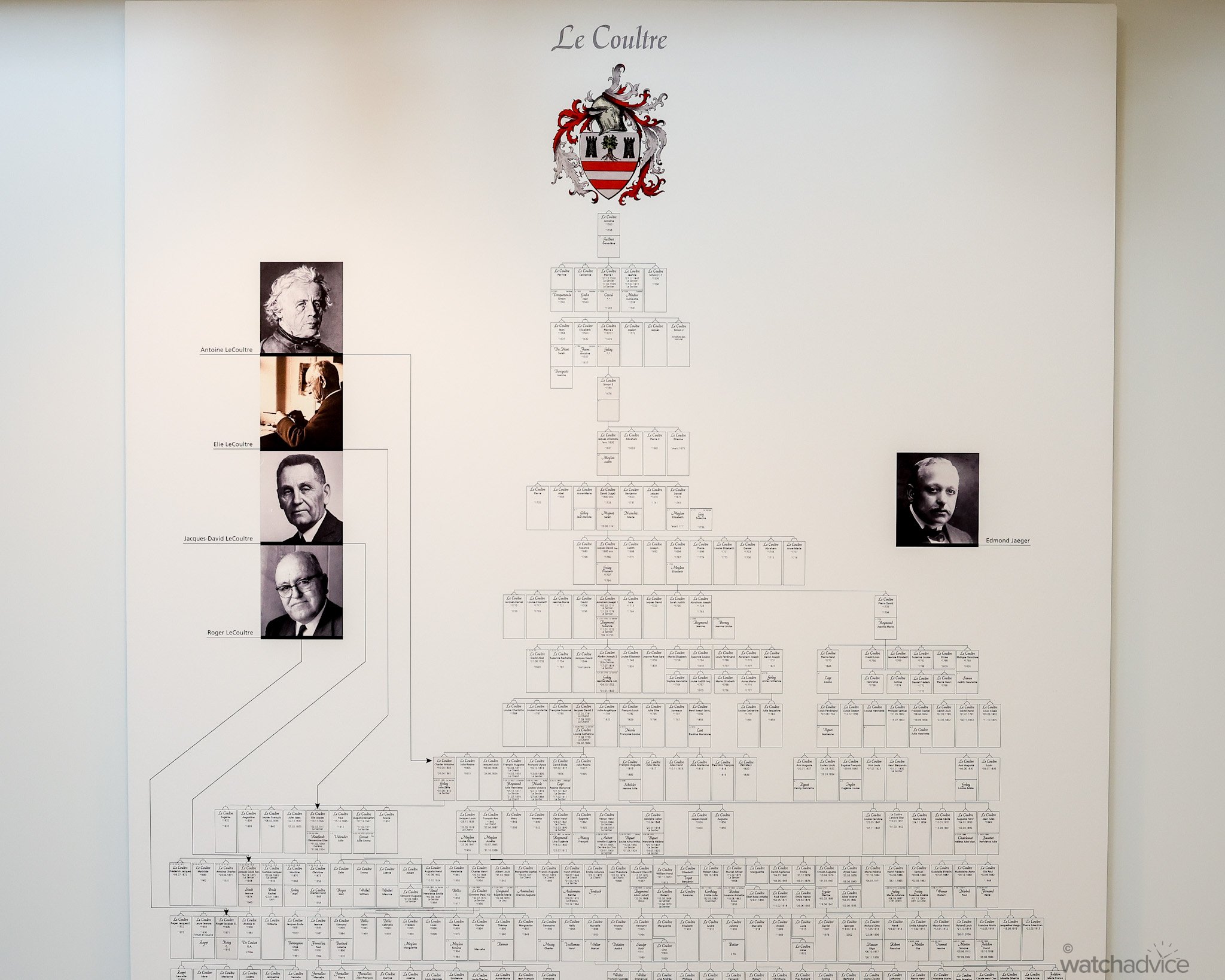
A few pieces that did stand out for me, however, was the Circa. 1900 Patek Philippe Pocket Watch for Tiffany. This is a pocket watch that is triple signed, meaning three different manufacturers came together to assemble and create the piece. It is unique and almost unheard of today! The pocket watch’s case was produced by Patek Philippe, the dial by Tiffany and, of course, the movement by Jaeger-LeCoultre.
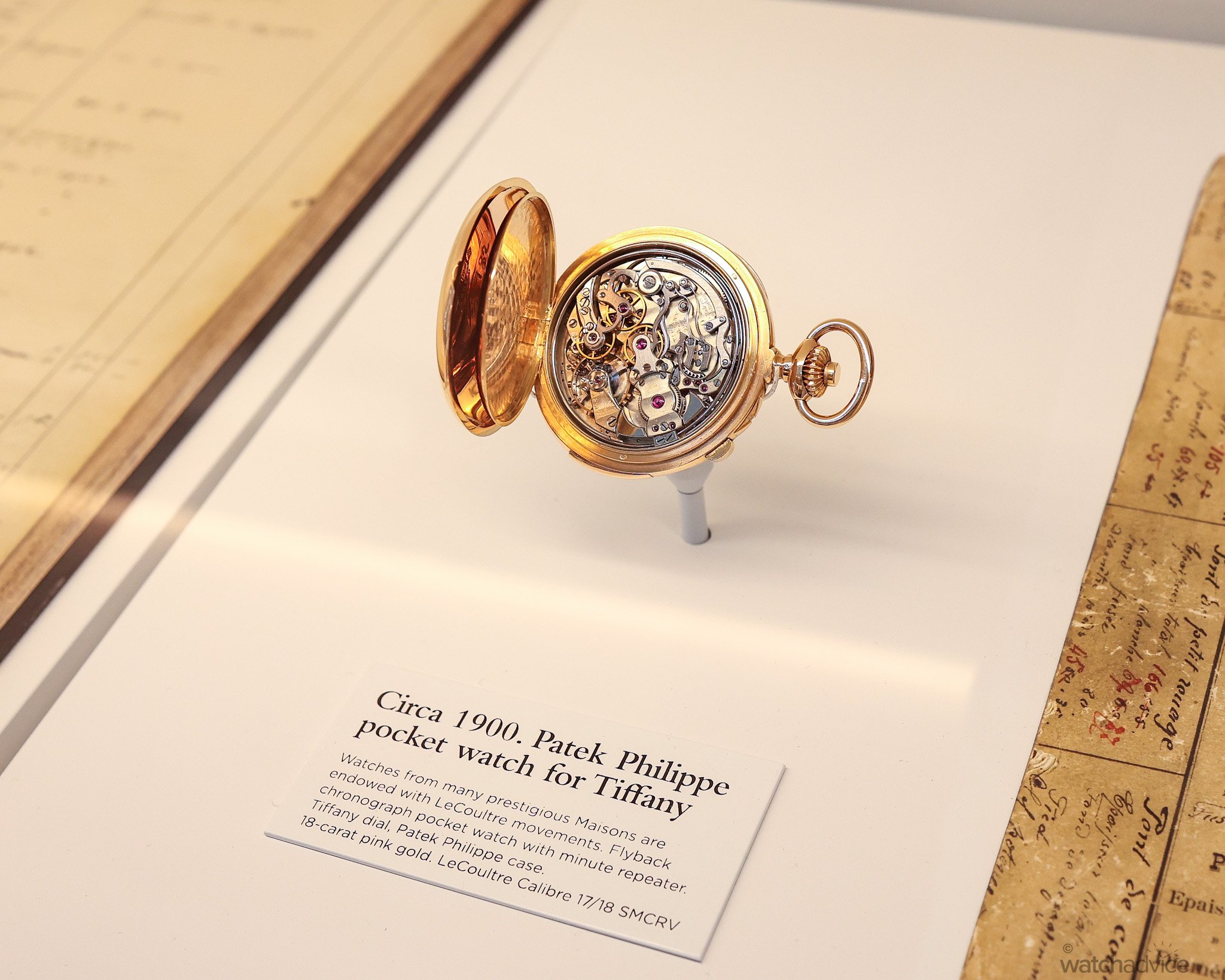
Another piece that stood out among the historic timepieces was the world’s “smallest” watch. If you think the ultra-thin movements these days are impressive, then this is sure to blow your mind! In 1929, Jaeger-LeCoultre created the world’s smallest mechanical movement (and, incidentally, watch) with the calibre 101. This record has not been broken to this day!
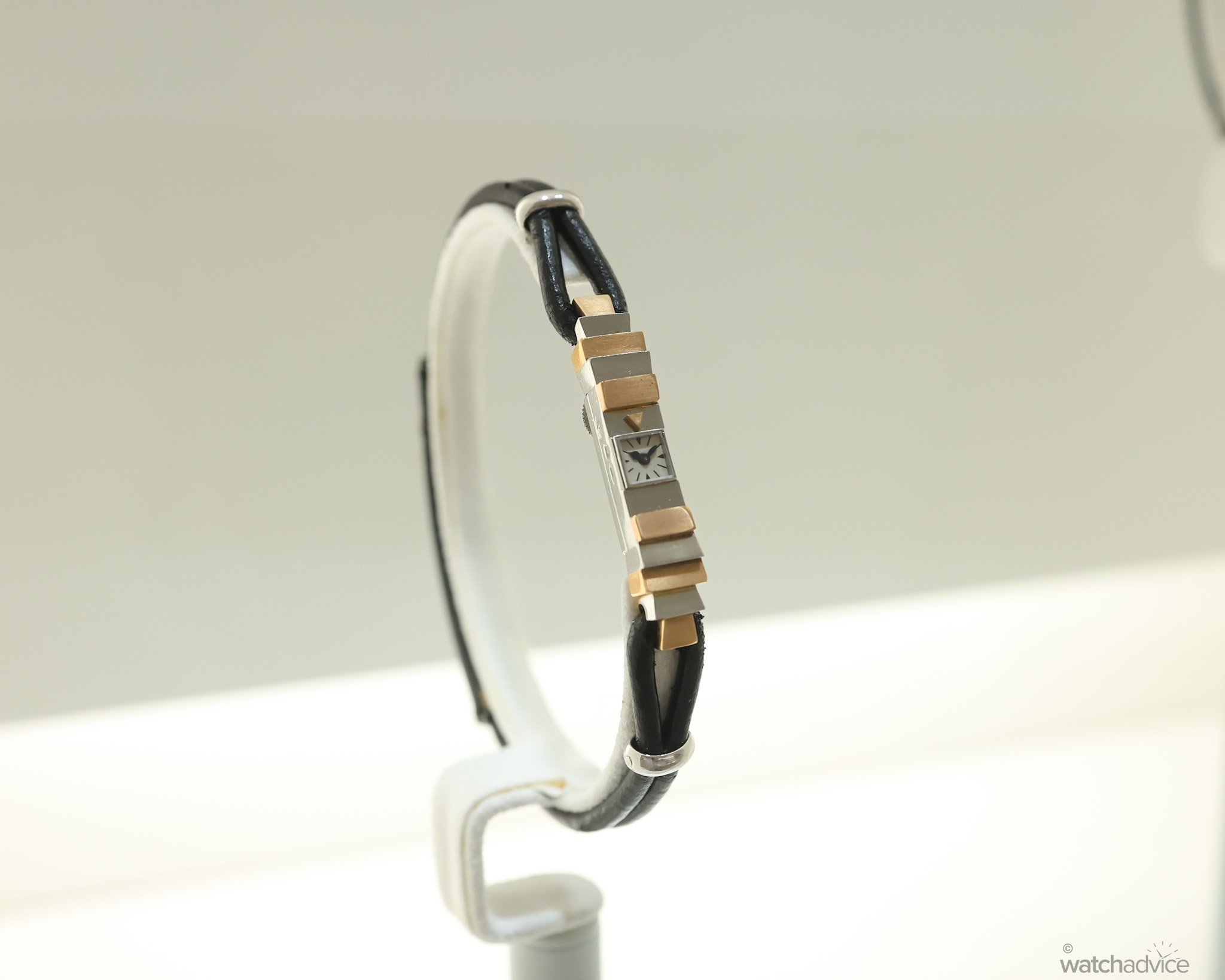
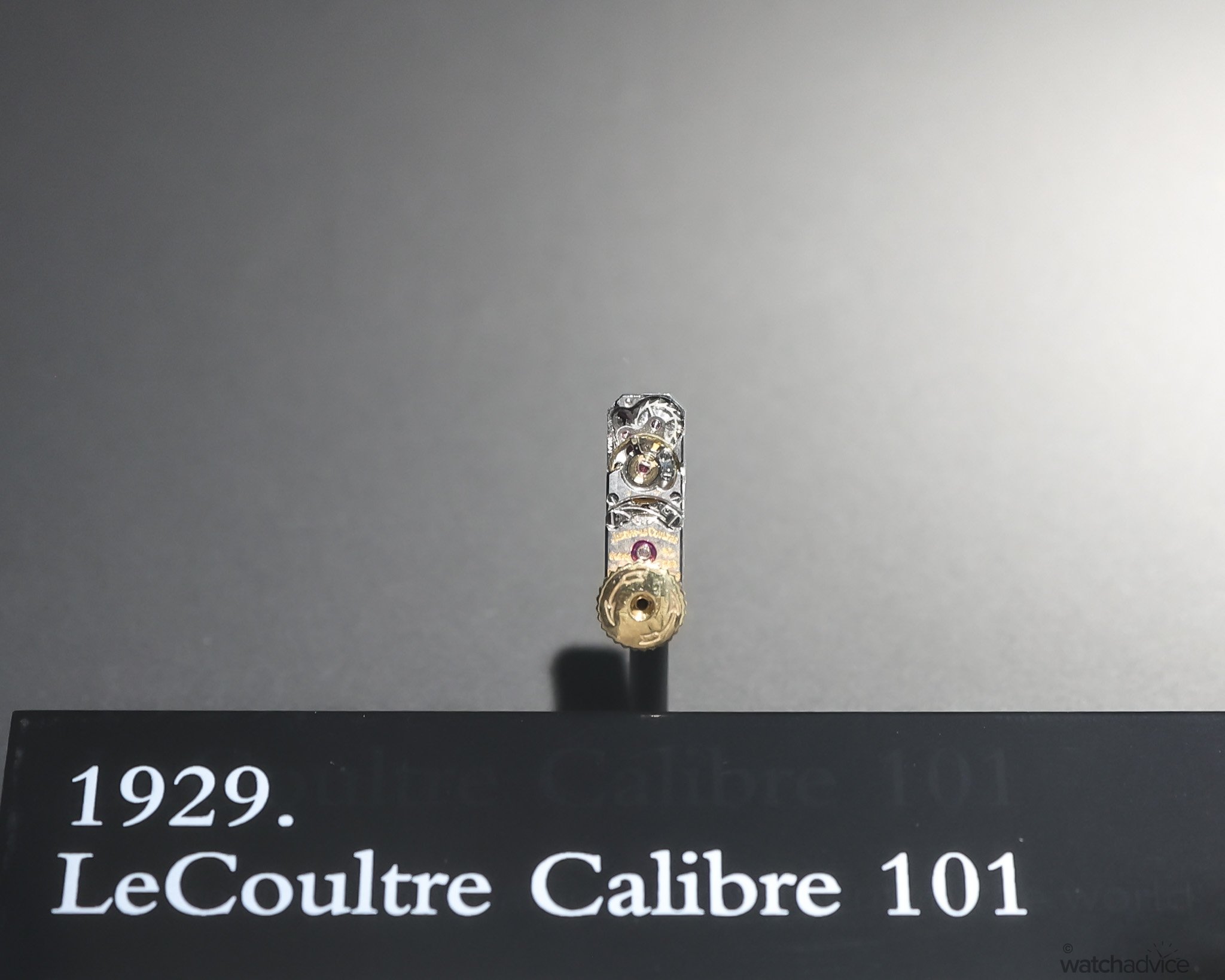
Alongside this, Jaeger-LeCoultre has a tremendous amount of historical pieces on show, all the way from some of the very first movements created, to the iconic Reverso from 1931, to modern-day pieces. It is a treasure-trove and something most watch enthusiasts would salivate over.
Historical Pieces
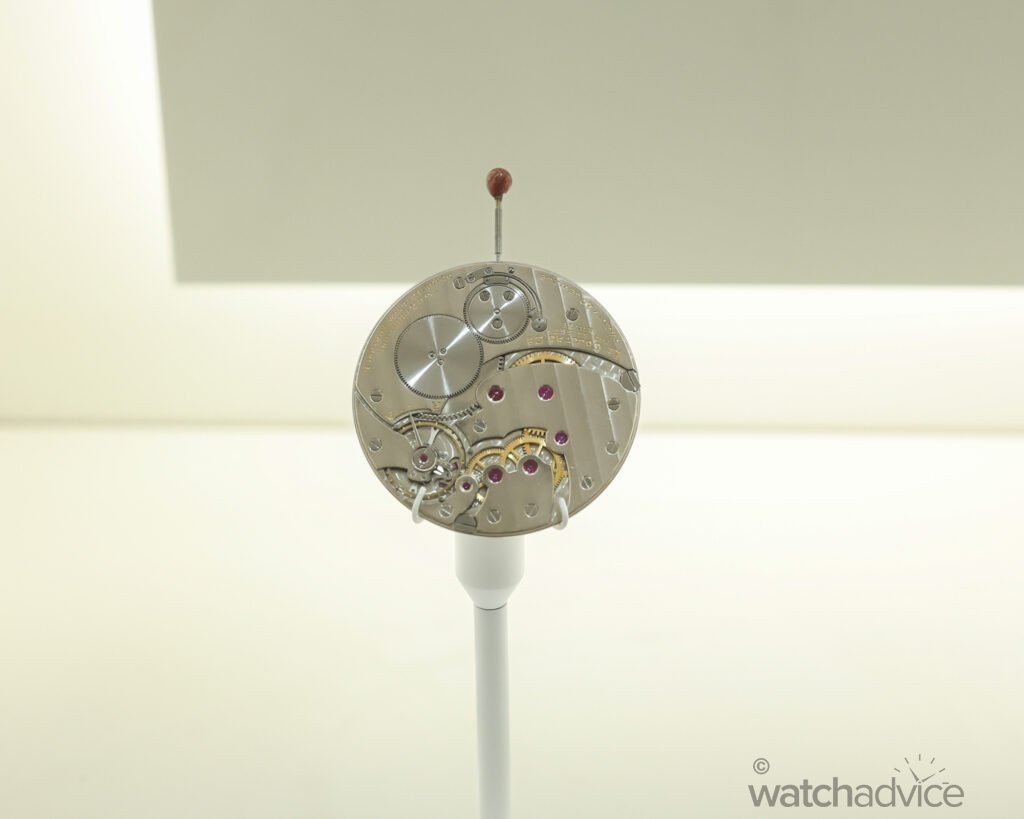
When Le-Coultre Met Jaeger
in 1903, Jacques-David LeCoultre met businessman, Edmond Jaeger – a french engineer and their collaboration gave birth to one of the greatest ultra-thin calibres in watchmaking and the birth of the Master Ultra Thin
Jaeger-LeCoultre Reverso (1931)
The Reverso was invented by Jaeger-LeCoultre in 1931 for the British army officers in India who wanted to protect the crystals on their watches while playing polo. As we know, the Reverso is a modern-day icon!
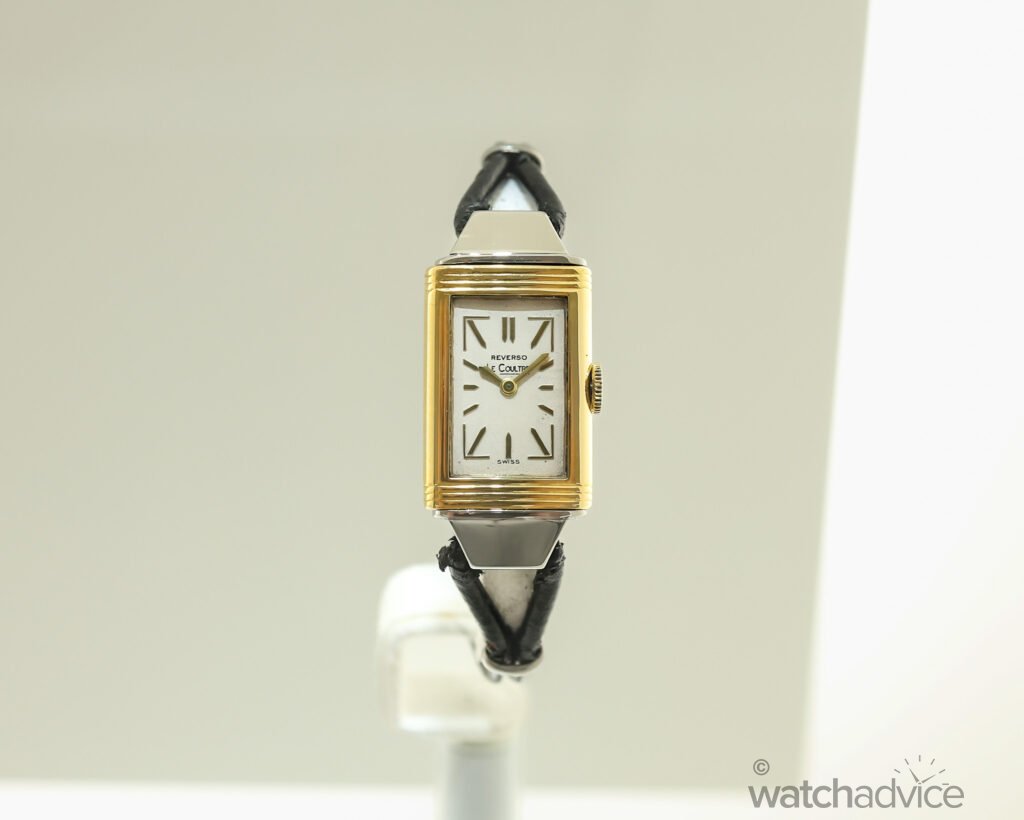
Heading Into Modern Day
Jaeger-LeCoultre Gyrotourbillon 1
In 2004, Jaeger-LeCoultre introduced the Hybris Mechanica Gyrotourbillon 1. This was the brand’s first grand complication timepiece. This is a watchmaking marvel, as the gyrotourbillon gravitates around two axis to counteract the negative effects of gravity in any position.
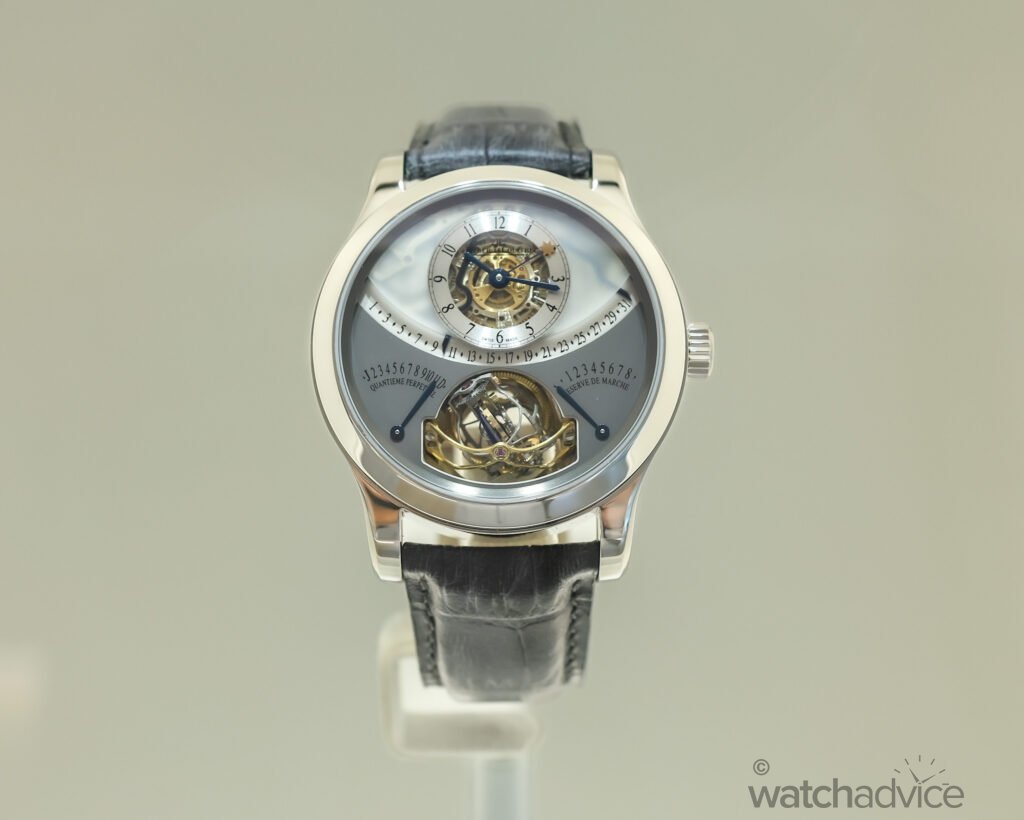
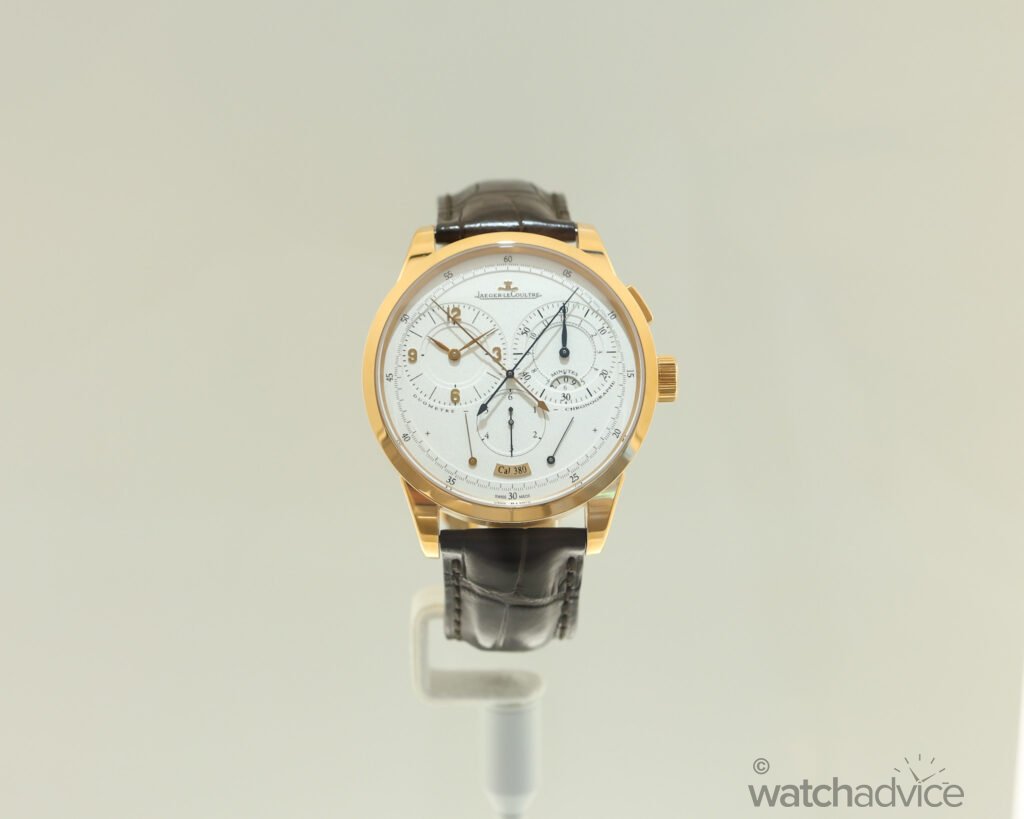
Jaeger-LeCoultre Duomètre à chrongraphe (2007)
In 2007, Jaeger-LeCoultre’s Dual-Wing concept was born. It was a genuine micro-mechanical revolution that made the whole Duomètre collection possible. The watch works by having two independent mechanisms which is united by a single regulating organ, guaranteeing excellence in performance and precision!
As we proceeded through the archived sections of the Heritage Gallery we came across arguably one of the most notable sections in Jaeger-LeCoultre’s Manufacture. When we entered this part of the Heritage Gallery, we were first greeted with a wall full of ATMOS clocks! This is where all the different Jaeger-LeCoultre ATMO clocks through the ages were showcased, from the ATMOS 1 in 1930 to the modern ATMOS Infinite created in 2022.
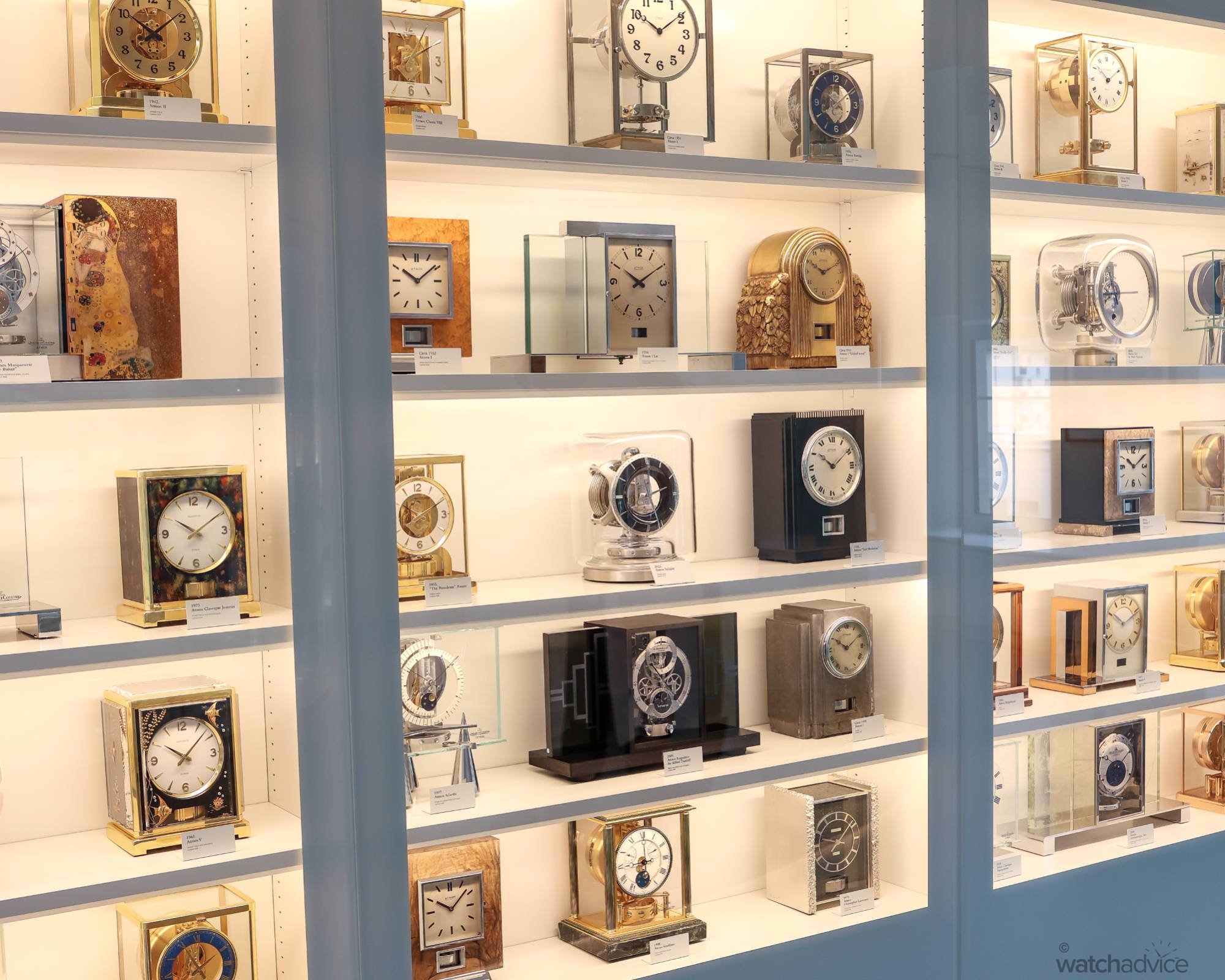
On the opposite side of the ATMOS wall was a spiral staircase that led to Jaeger-LeCoultre’s manufacturing departments. This staircase was quite remarkable, however, as it was decorated with watch movements in a very aesthetically pleasing manner. The glass casing of the staircase featured movements that were placed in a spiral arrangement to mimic the design of the staircase. The movements shown are what Jaeger-LeCoultre have used to date, going all the way back to the brand’s first pocket watch movements.
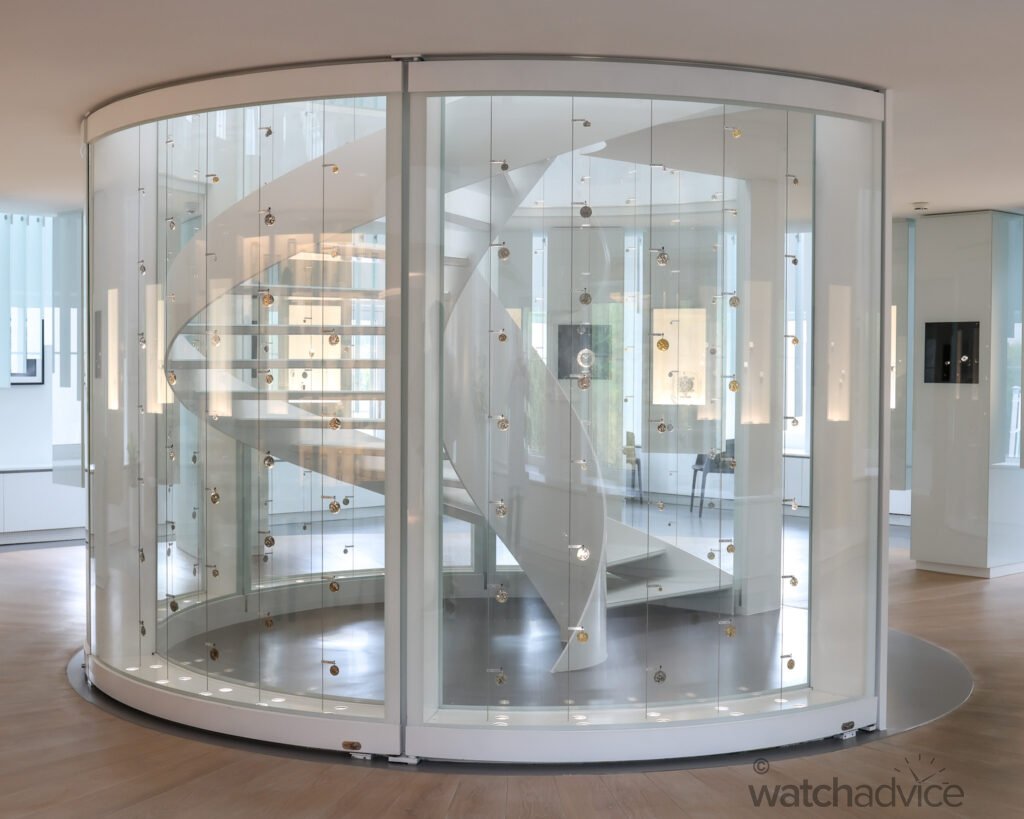
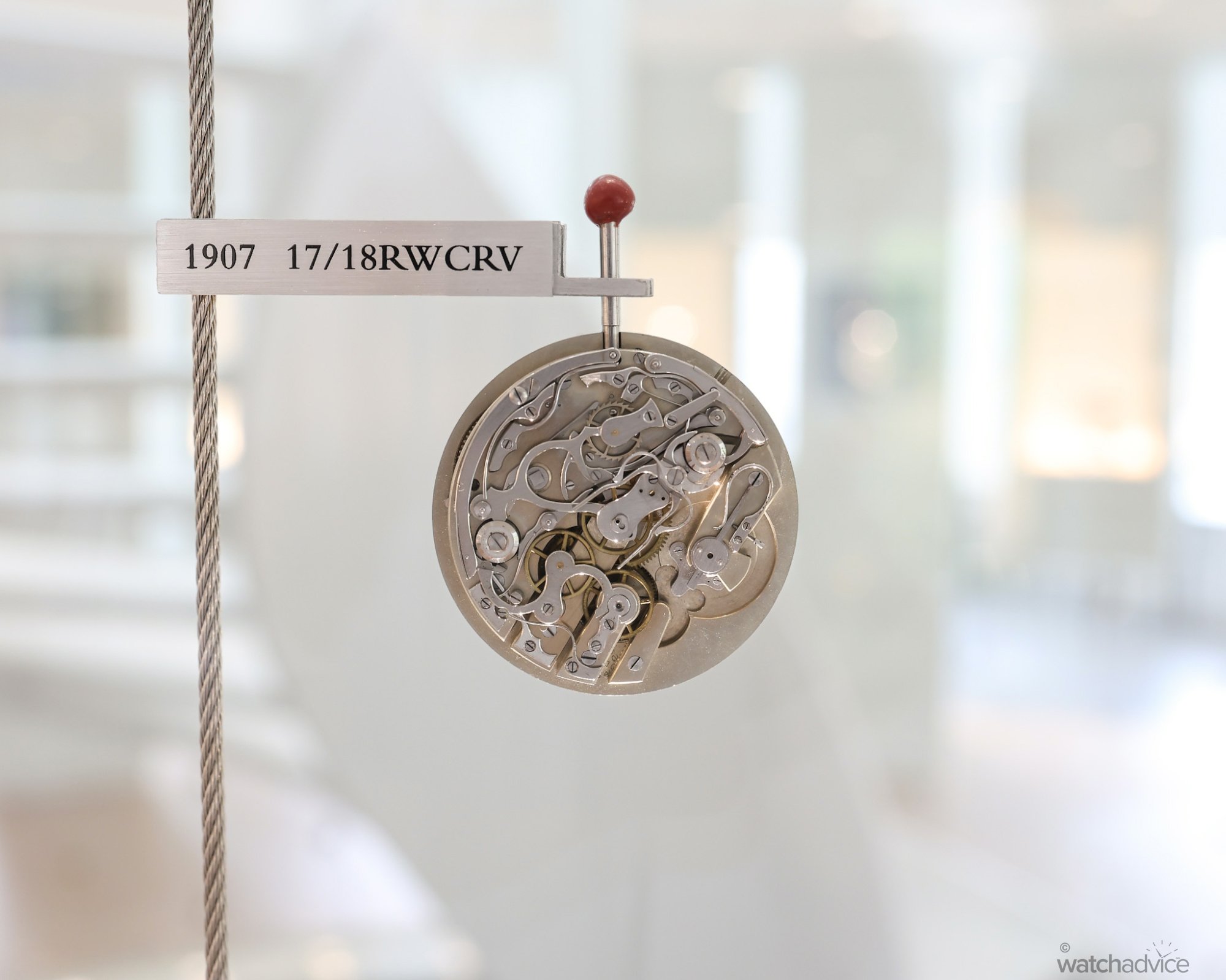
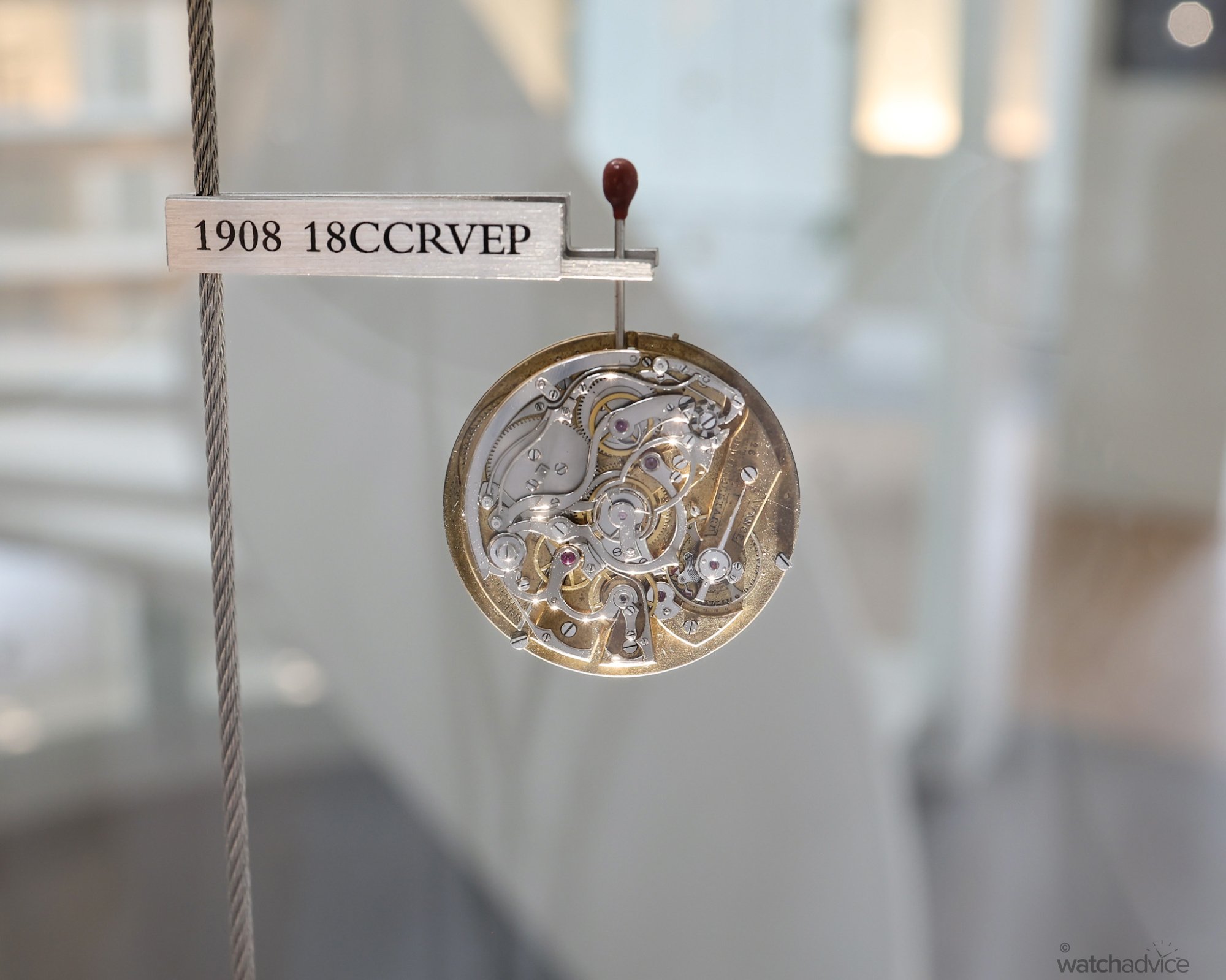
As we made our way upstairs through the spiral staircase, the first thing we noticed when we reached the upper floor was the watchmaker’s desk, which had various tools used to adjust the movement and fix the dials onto the timepieces. An interesting fact about the desk shown in the photos below is that Antoine LeCoultre used it from his original workshop! Check out Jaeger-LeCoultre’s video on “The Genesis of Precision” to see an animation of Antoine LeCoultre using some of these tools and machines!

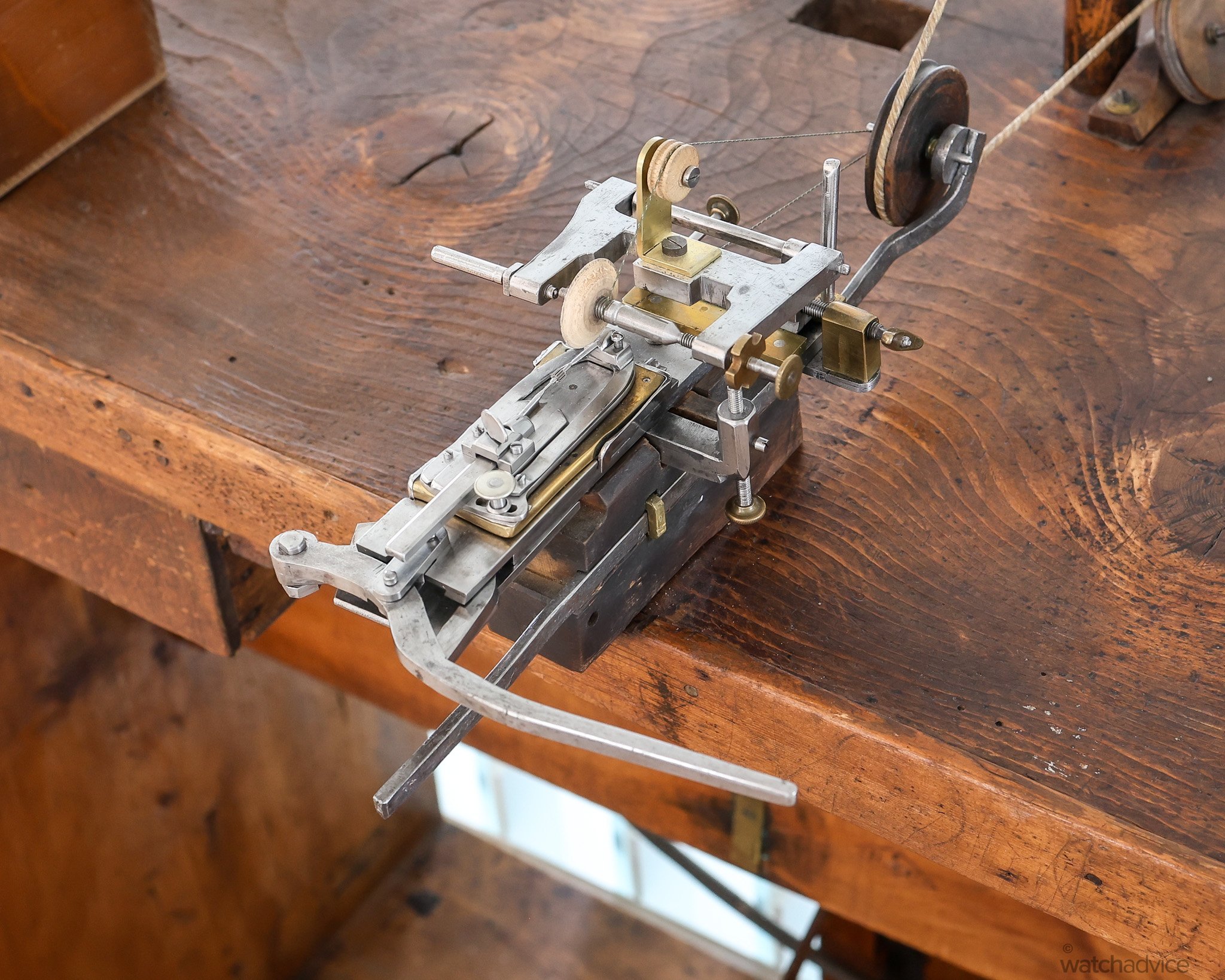
The next part of the Jaeger-LeCoultre Manufacture visit involved walking through the watchmakers’ various workshops. One of the first ones we passed through was the watch restoration and repair section, and although we didn’t get to be up close and talk to the watchmakers, we still got to see them hard at work!
Our Jaeger-LeCoultre Manufacture guide took us to a department where “dial stamping” was executed. There, an expert watchmaker took us through a presentation (with television imagery!) of the process of stamping the dials. We were shown the beginning to end of dial stamping, including physical pieces of each of the different stages in the stamping process. The final product is the dial that is used for the Master Grande Tradition Calibre 948!
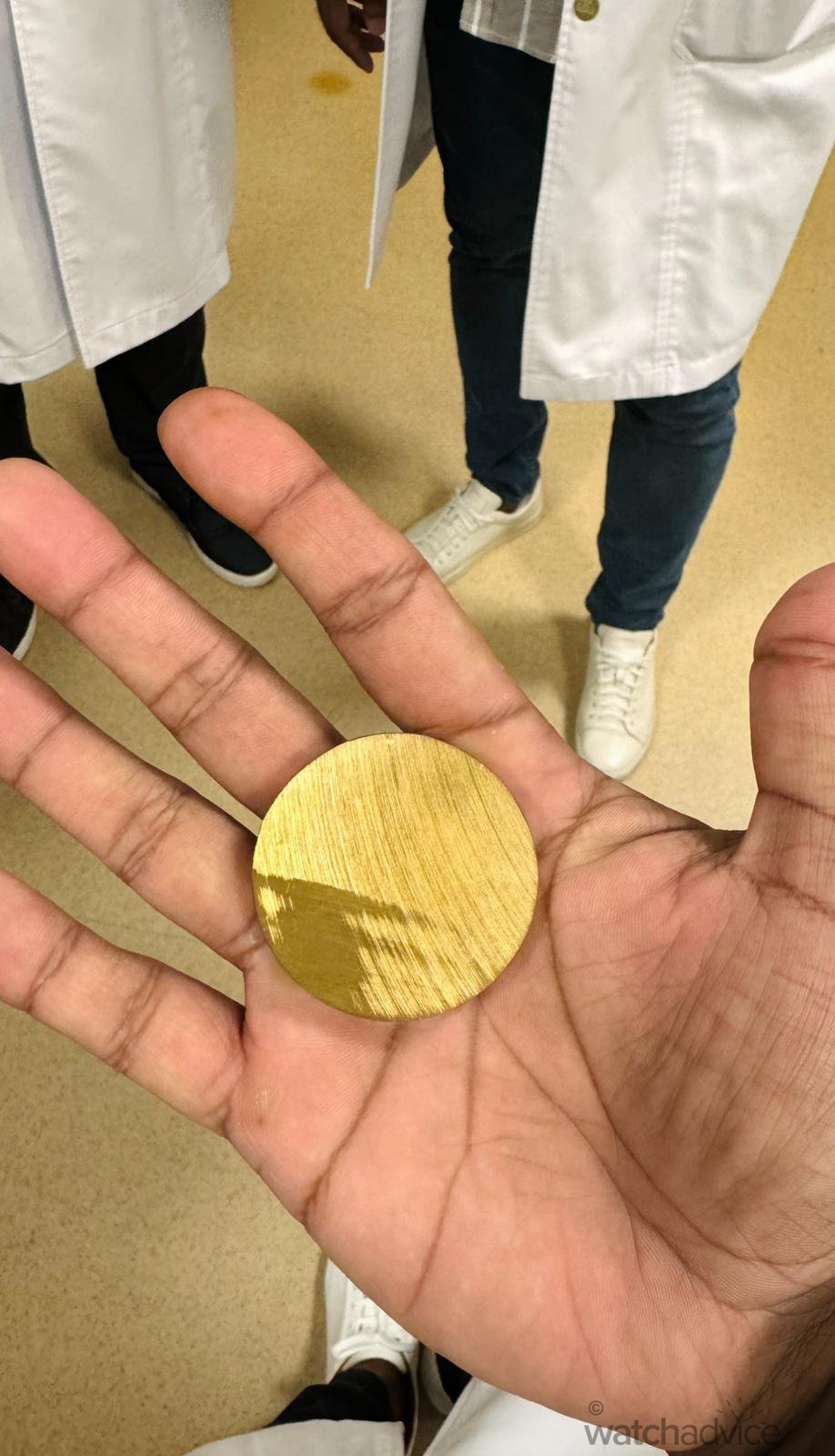
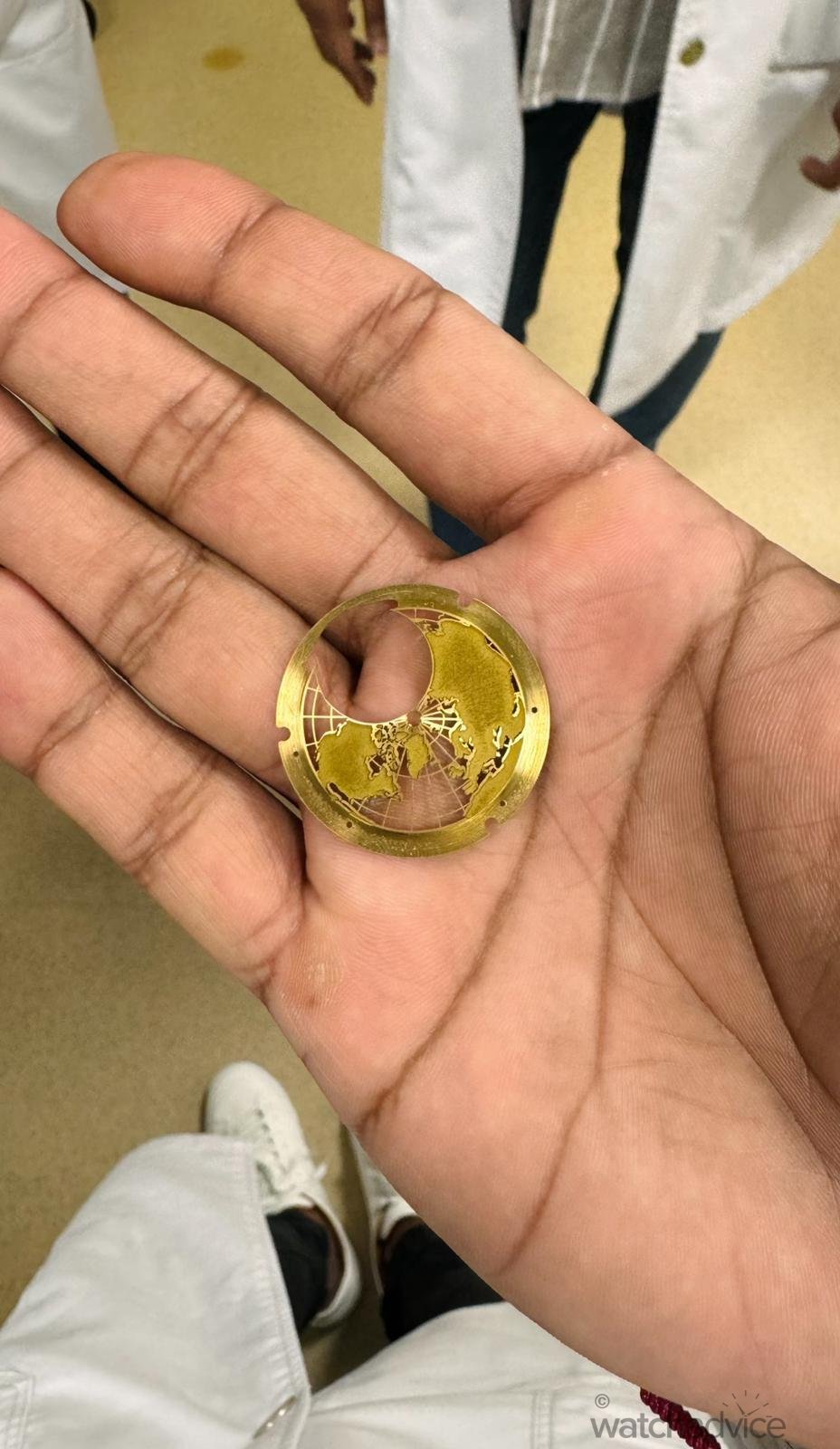
From there, we briefly looked at the material’s storage section of the Jaeger-LeCoultre Manufacture. This is where they keep all the metal sheets, spare parts, and waste. From this point, we then walked to the manufacture’s high-complication section, a place that I was probably looking forward to the most in this tour! I mentioned earlier how large the Jaeger-LeCoultre Manufacture is from the outside, but when you have actually to go through the different sections, it is indeed quite a walk (the entire manufacture is equivalent to almost walking 11km!), so make sure to wear walking shoes!
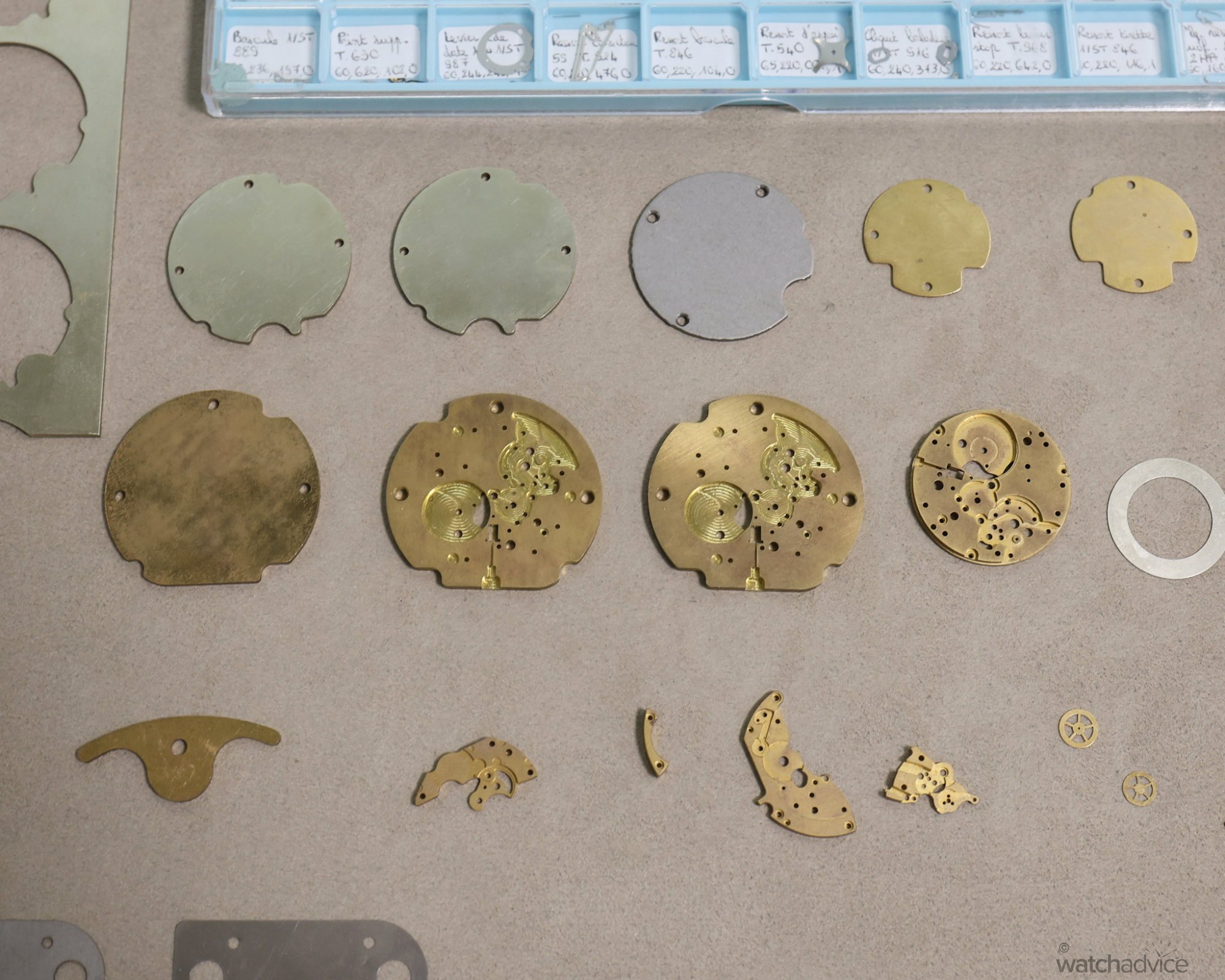
The Jaeger-LeCoultre’s high-complication department was next and it was only I was quite looking forward to seeing. While we couldn’t go inside due to them working on new timepieces and proprietary information, we still had the privilege of seem them work through the windows. I must say, it was quite the team in this department, which seemed substantially larger than the other sections of the Jaeger-LeCoultre Manufacture.
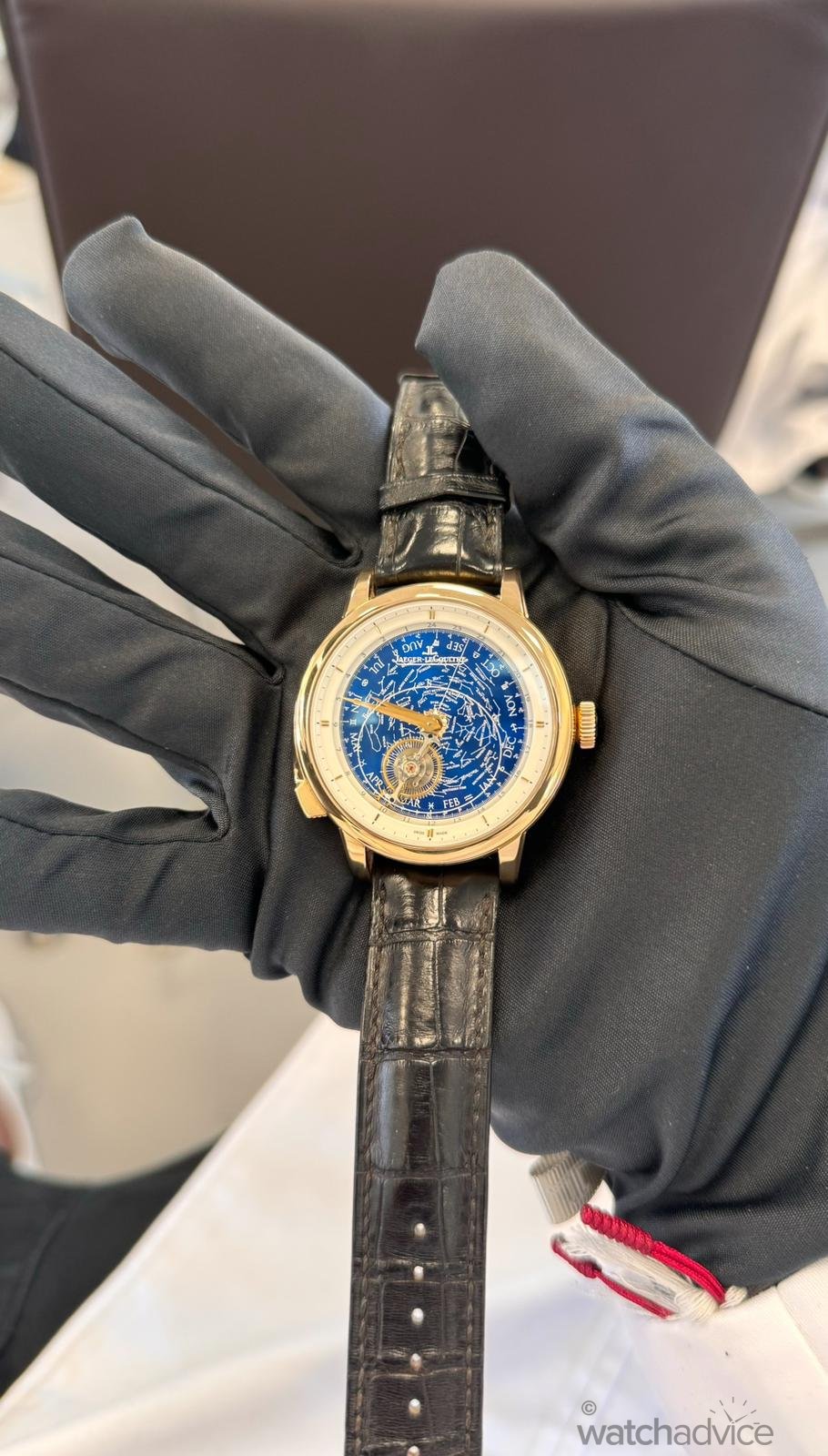
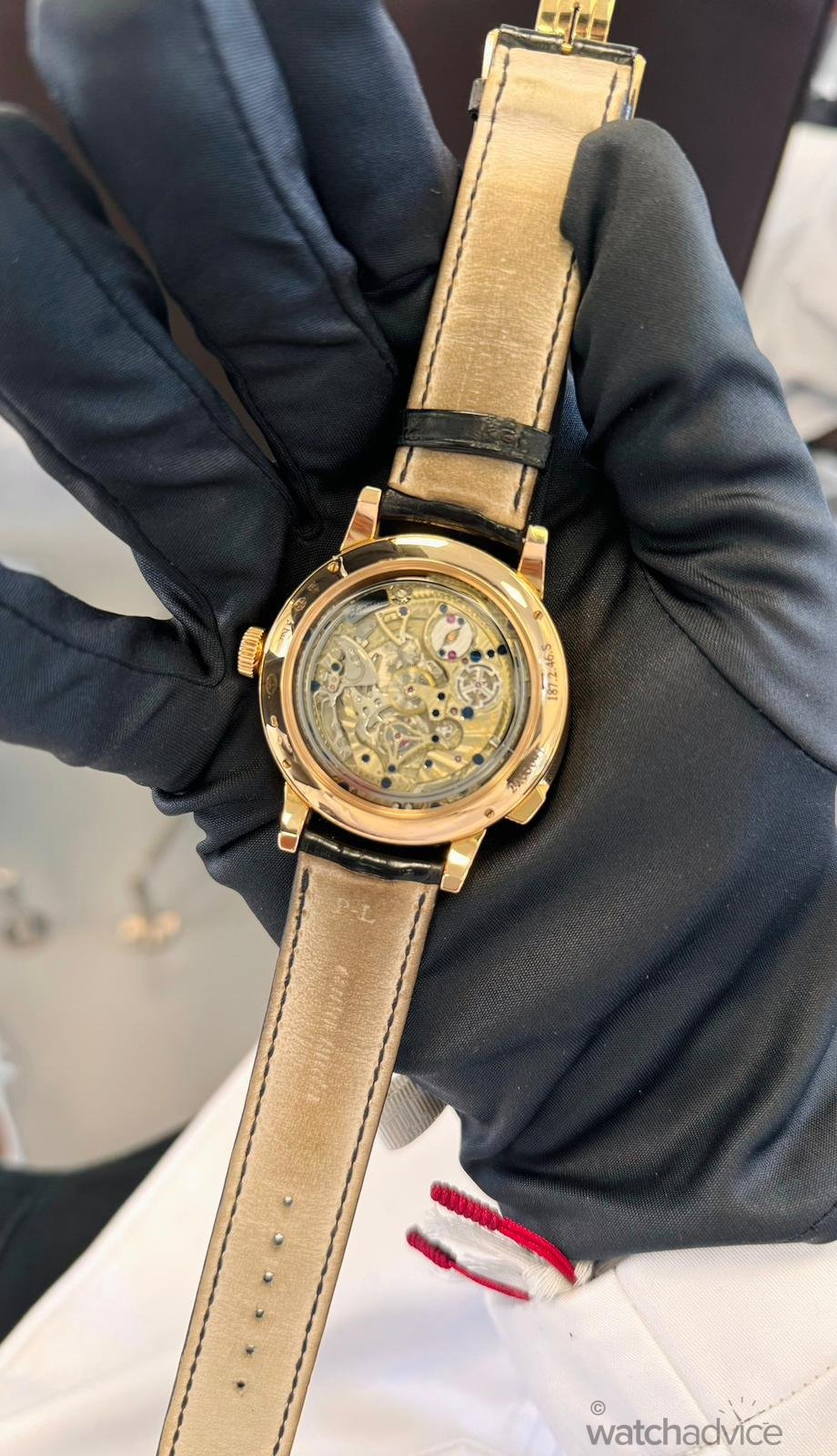
Nestled in the middle of the high-complication department (we were still sitting outside the department, however), we were given a presentation once again with a watchmaker who explained to us what this department was about. We also got a hands-on feel with three of Jaeger-LeCoultre’s high-complication timepieces. The first was the Jaeger-LeCoultre Master Grande Tradition Grande Complication timepiece, which honestly is one of the most incredible timepieces I’ve had the pleasure of holding. The watch has a celestial chart on the dial, highlighting all the different star patterns and a revolving tourbillon that moves around the dial! Oh, and it also comes with a minute repeater complication that we also engaged to hear the beautiful chime!
The second timepiece was the Jaeger-LeCoultre Polaris Perpetual Calendar. Fortunately, I’ve had the chance to hold and try this piece on already; however, I certainly wasn’t going to pass up the chance to see this masterpiece again. The last timepiece was another one that was breathtaking to hold and by far my favourite so far. The Jaeger-LeCoultre Reverso Tribute Gyrotourbillon is a watch that I personally thought I’d never get the chance to hold!
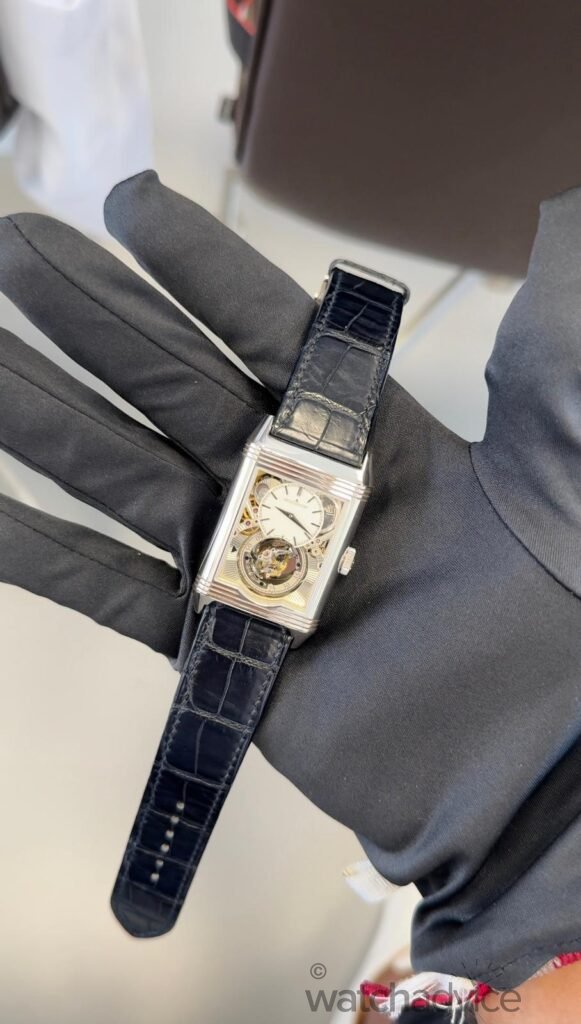
The Reverso Tribute Gyrotourbillon is an engineering masterpiece, and seeing this timepiece towards the end of the Jaeger-LeCoultre Manufacture visit made it all the more special. Seeing the gyrotourbillon in action for me is an amazing piece of watchmaking, and the fact that it’s on a Reverso, whereby we can see the second “dial” that is a skeletonised version of the front, makes this timepiece even more exceptional!
The last part of the Jaeger-LeCoultre Manufacture tour took us to the ATMOS atelier. This is where they create and test all the ATMOS clocks before they hit the shelves in retail stores and Jaeger-LeCoultre boutiques. Our tour guide gave us a fascinating demonstration of how the ATMOS clock keeps a continuous power reserve. The simplest explanation is that the clock generates energy through very minor temperature changes. Within a sealed capsule at the back of the ATMOS clock, there is a mixture of gas that expands and contracts as the temperature changes, allowing the “movement” to wind naturally. The demonstration showed us that an expanded capsule quickly contracts when it’s exposed to a different temperature, such as ice water.
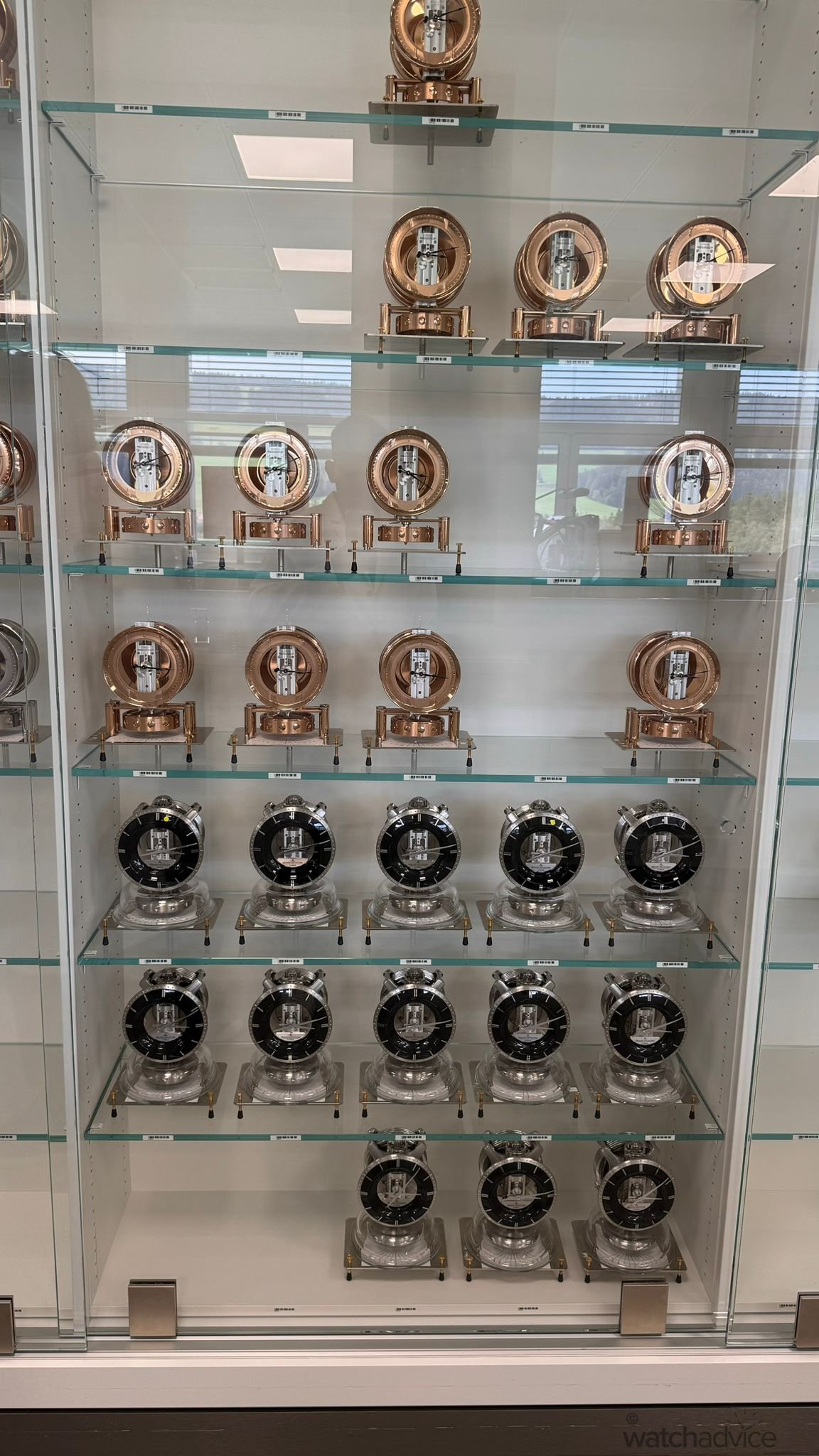
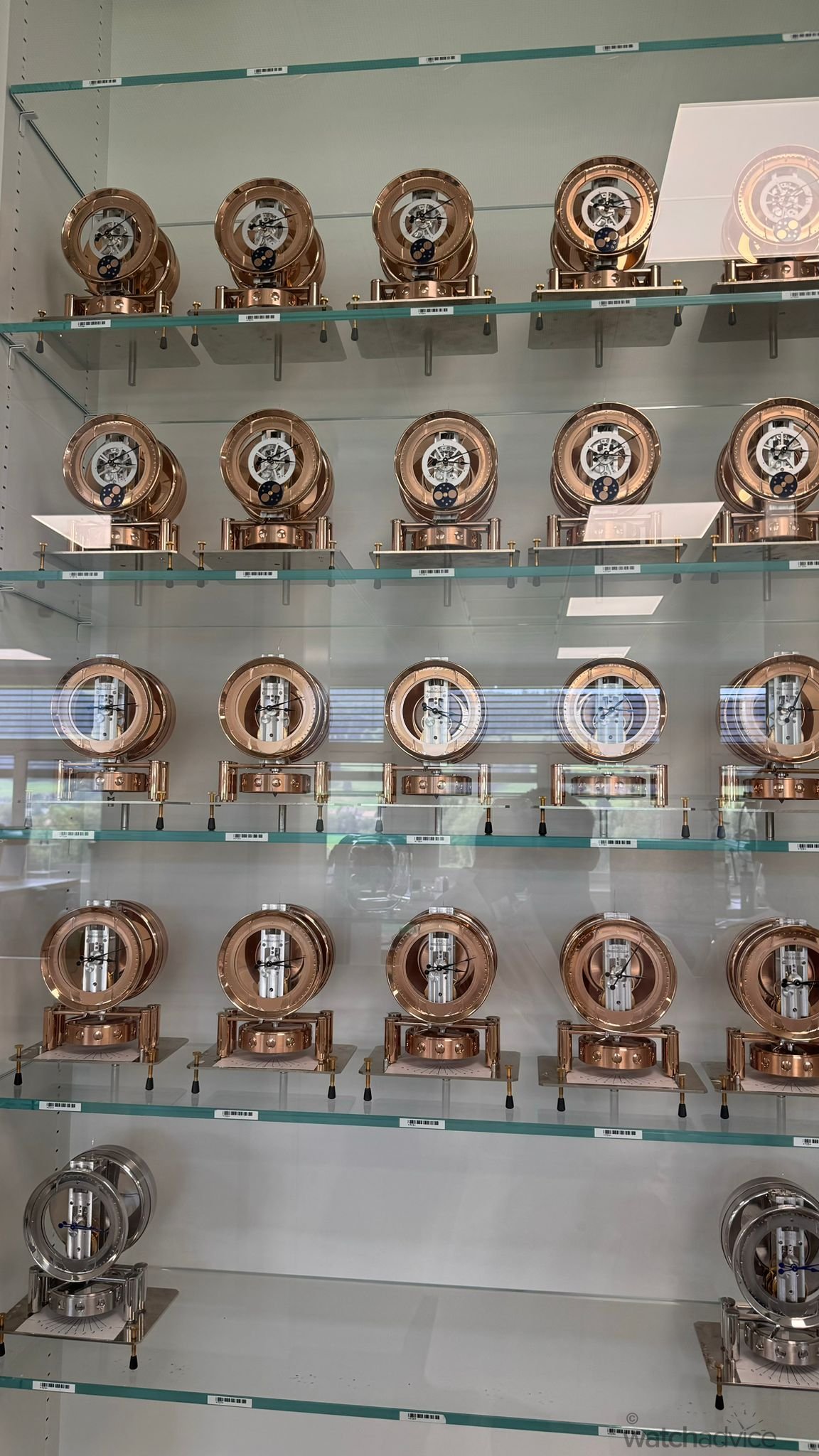
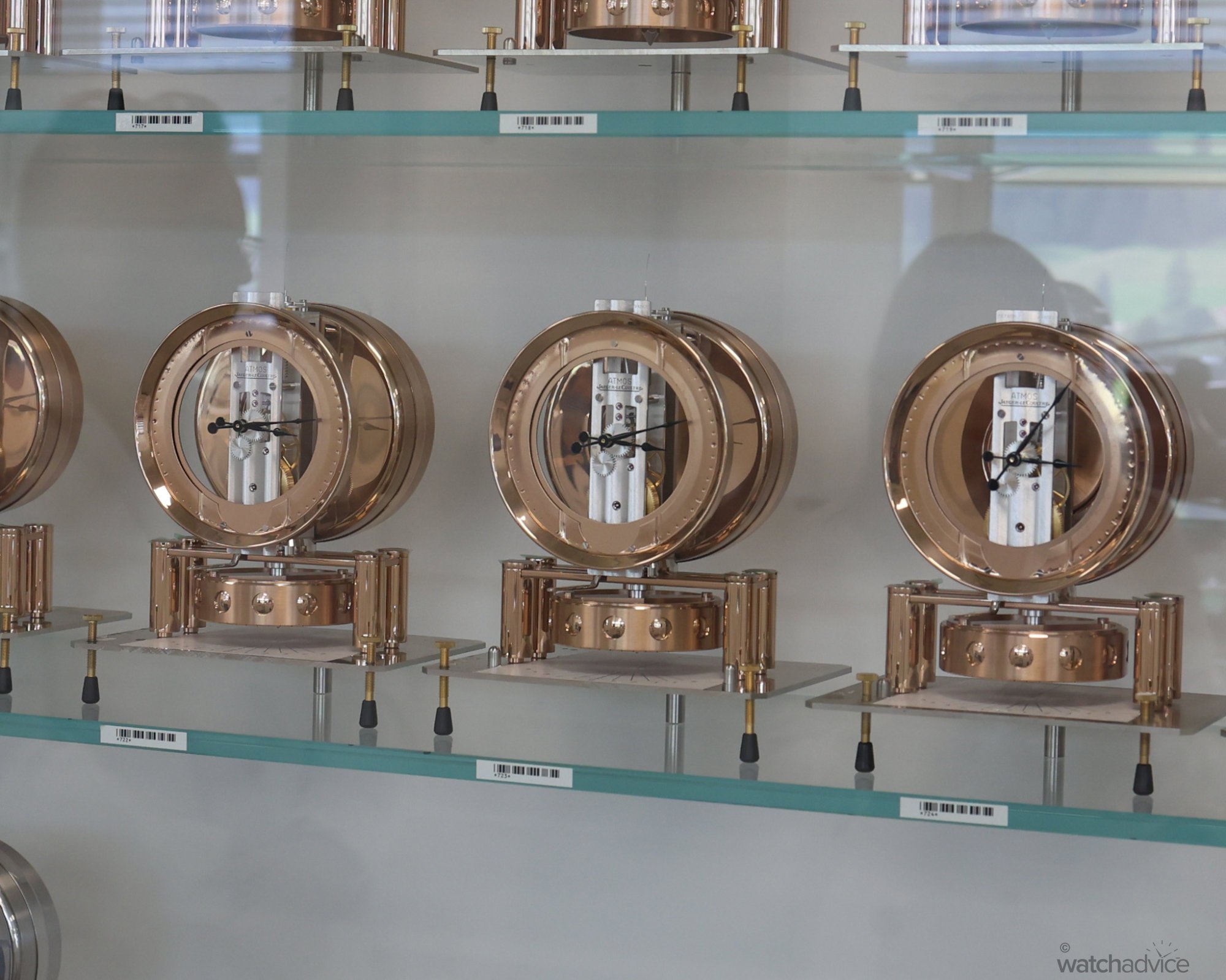
As the Jaeger-LeCoultre Manufacture visit came to an end, it became increasingly clear to me that the true value of a luxury timepiece was not measured by the materials used or the brand name engraved on the dial. After witnessing first-hand Jaeger-LeCoultre’s relentless pursuit of perfection in every part of the manufacturing process, from the hand-finishing of movements to the intricate assembly of the complications, it’s easy to understand why the brand’s watches carry such a premium.
If you have ever wondered why a luxury watch commands its price, a visit to the Jaeger-LeCoultre Manufacture will quickly make you understand in a way that words simply cannot! For me, it was an experience that changed the way I see not just the brand and their timepieces but the whole concept of watchmaking itself. After leaving the Grande Maison, I had a deeper appreciation for the art of Swiss watchmaking, along with a knowledgable respect for the skill, passion and time it takes to create Jaeger-LeCoultre timepieces. Now I know why they are the watchmaker’s watchmaker.